Occupational Safety, Security and Accident Prevention
1. Management System
(1) Safety Philosophy and Approach
Realizing a Company where Employees can Work Safely, with Peace of Mind, and in Good Health
We regard safety as the foundation of business continuity. As such, we are working on safety as a key management issue necessary for corporate growth.
Under our safety philosophy and policy as well as the Course of Action for achieving them, we strive to be a company where all employees work safely and experience happiness, and as a responsible member of the community, we will carry out environment- and safety-conscious business activities.
We also implement safety activities at our Group companies in Japan and overseas based on our safety philosophy and policy. The entire Group works together to ensure safety.
Safety Philosophy
At JSR Corporation, safety is our highest priority and the foundation of all of our activities.
Accordingly, we will create safe worksites and strive to maintain physical and mental health, with the goal of ensuring workers happily take it for granted that they will return home safely at the end of each workday.
Safety Policy
- Extremely Safe Behavior
The Safety Policy has penetrated through the organization, the Course of Action is established as applying to everyone, and safety competency is improving through proactive safety activities. - Enhanced Human Resources and Organizational Strength
High personal skills, organizational ability, and a healthy organizational culture are being maintained with the establishment and execution of the education and training programs needed for organizational management. - Optimal Risk Management and Security Measures
Security measures corresponding to risk importance are being efficiently and effectively implemented using new technologies.
Courses of Action of Safety
- No matter the situation, we will act with safety foremost in mind.
- We will comply with established rules and never fail to act in accordance with safety basics.
- We will maintain safety by identifying and eliminating both actual and potential hazards.
- We will strive to create comfortable work environments and promote physical and mental health.
- Through communication and ingenuity, we will aim to achieve 100% employee participation in all safety activities.
(2) Safety Management System
JSR Group strives to minimize risks in occupational safety, security, and accident prevention efficiently and effectively by steadily implementing the PDCA cycle based on a Safety Management System that has been configured according to the circumstances of each business site.
To verify the effectiveness of this management system, our business sites conduct internal audits, safety patrols, and management reviews. In addition, the JSR Headquarters Environment and Safety Division conducts Headquarters Environment and Safety Audits in an effort to achieve continuous improvement.
We have compiled manuals to ensure appropriate and effective response measures to prevent damages from spreading in the event of an accident or disaster. By conducting regular drills based on these manuals, we have established a system capable of properly handling emergencies.
In addition, to prevent recurrences, we thoroughly investigate all accidents to determine the root cause, implement countermeasures, and verify their effectiveness. In turn, we share this information within the Group to stop similar accidents and injuries before they occur.
We believe that human resources with high safety awareness are essential for implementing reliable safety management and effective safety activities, so we are also working on human resource development.
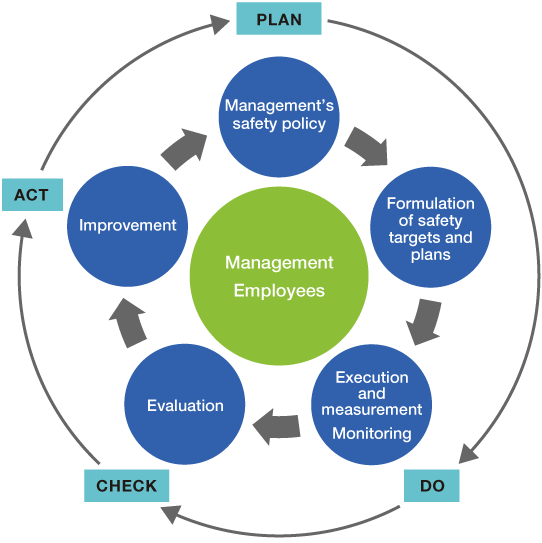
2. Targets and Results
JSR Group uses a selection-and-concentration approach to implement more efficient occupational safety, security, and accident prevention efforts by effectively reflecting the results of analysis of safety activity performance at each business site and internal and external safety-related information in its activity policies and targets for subsequent fiscal years.
We have set the number of occupational and facility accidents as a result of our safety activities as a key performance indicator (KPI) of the material issue of “health and safety” within the Group. We have also globally standardized the evaluation criteria and conduct monitoring.
KPI | Aggregation scope*3 | 2023 | 2024 | ||
---|---|---|---|---|---|
Target | Result | Judgment | Target | ||
Number of occupational accidents*1 | JSR Group | 2 or fewer | 4 | Not achieved | 2 or fewer |
Number of facility accidents*2 | JSR Group | 0 | 0 | Achieved | 0 |
*1. Occupational accident resulting in four or more days of lost time
*2. Explosions, fires, leaks, or any of the following that are recognized as accidents by the government:
・ Accidents or disasters that cause health hazards to employees or local residents
・ Accidents or disasters with estimated damages exceeding 100 million yen
・Accidents or disasters that shut down a part of the plant for more than a month or the entire plant for more than a week
*3. Domestic or foreign companies in which JSR's shareholding exceeds 50%
Occupational Safety
In Japan, JSR Group defines occupational accidents resulting in four or more days of lost time, which must be reported promptly to the government, as “serious occupational accidents.”
In 2023, the JSR Group had four serious occupational accidents, the same as the previous year, falling short of its target of two or less. There were no accidents at JSR, but there were two involving employees of Group companies in Japan and overseas, and two at contractors.
We will continue to work to eliminate similar accidents using the results of our analysis, including non-serious occupational accidents, and to eliminate occupational accidents by fostering a solid safety culture of safety awareness and safe behavior globally.
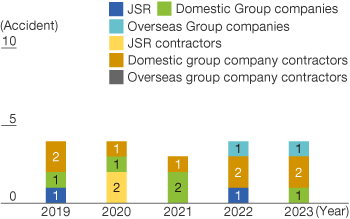
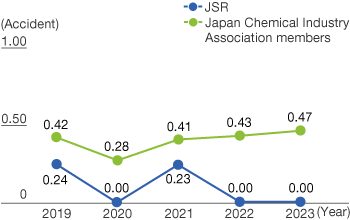
*Until 2021, the scope was the Yokkaichi, Kashima, and Chiba plants with JSR manufacturing facilities. In 2022, the scope was narrowed to the Yokkaichi Plant with JSR manufacturing facilities.
Security and Accident Prevention
2023 Security and Accident Prevention Target: Zero Serious Facility Accidents
JSR Group defines significant facility accidents as accidents involving explosions, fires, leaks, and other incidents recognized as accidents by the government corresponding to high-urgency events outlined in the Risk Management Regulations.
There were no serious facility accidents within JSR Group in 2023, achieving the target of zero.
On the other hand, the number of minor non-serious facility accidents has been on an upward trend from the previous year. Much of this was due to the way equipment was managed and the way the installation work was carried out. To this end, we will work to eliminate facility accidents by utilizing the results of analysis in the same way as we address occupational accidents, and by fostering a steady safety culture of safety awareness and safe behavior globally.
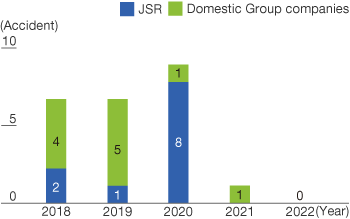
* Until 2021, accidents were counted based on the definition of "abnormal phenomenon" under the Act on the Prevention of Disaster in Petroleum Industrial Complexes and Other Petroleum Facilities. From 2022, accidents involving explosions, fires, leaks, and other incidents recognized as accidents by the government corresponding to high-urgency events outlined in the crisis management manual are counted.
3. Safety initiatives
Top Management’s Commitment to Safety
Top management of JSR communicates their thoughts on the importance and value of safety to employees on various occasions, such as those below.
- Instruction at the beginning of the calendar and fiscal years
- Direct address during entrance ceremony
- Instruction during National Safety Week
- Instruction during JSR Safety Day
- Instruction in Headquarters Environment and Safety Audits
Thorough Risk Management
JSR Group emphasizes risk assessment as a means of preventing accidents and disasters and ensuring safety. By steadily implementing risk assessments, we are working to ensure effective risk management.
In FY2023,we confirmed that the business sites and companies with the Group’s manufacturing facilities were each engaging in risk management in accordance with their respective standards.
We believe that it is necessary to evaluate serious risks that have a significant impact on management using the same criteria in order to check the entire Group, including overseas, side-by-side. Currently, we are carefully examining the risks identified at each of the Group's sites and reviewing criteria.
JSR manages risks related to chemical substances, facilities, and occupational safety from research and development to each stage of the plant life cycle. We have defined the items and procedures necessary for such management within our standards.
Furthermore, not only do we verify risks when introducing new facilities or making changes but we also identify risks in existing facilities using various approaches. We engage in centralized management of those risks that have the potential to lead to accidents or disasters, and we have established an environment where any employee working at a business site can check the description of risks, the status of countermeasures, and the status of emergency responses carried out until permanent countermeasures can be implemented.
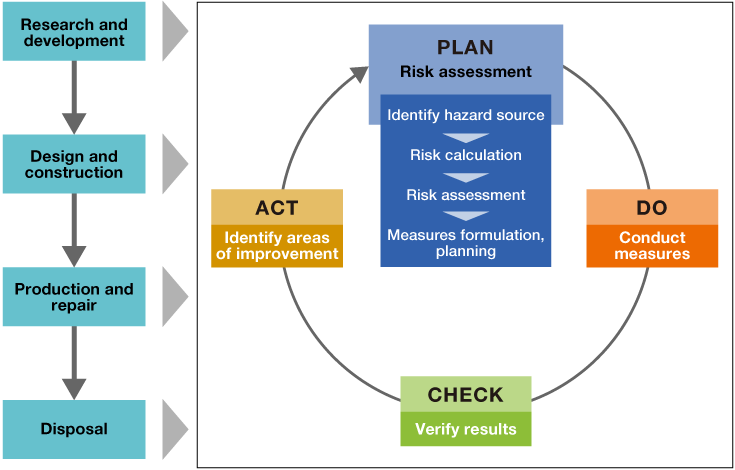
JSR Group’s Shared Safety Concept
JSR Group’s Shared Safety Concept
Achieving zero accidents and injuries requires that we improve the safety level of the Group. In addition, we believe that it is important to understand and act on the Group's shared safety concept in order to address this issue as a whole.
In 2023, JSR Group formulated the JSR Group’s shared safety concept, which adds the concept of risk to the existing safety, safety infrastructure, and safety culture. We are now working to disseminate this philosophy to employees in Japan and overseas. In 2023, we held e-learning at all domestic business sites and some overseas locations, with a high participation rate and correct answer rate on comprehension tests. In 2024, we plan to expand this to other overseas business sites.
Safety Level Assessment System
In 2023, JSR Group launched an assessment system that can quantify the level of a safety infrastructure and safety culture that is part of the JSR Group's shared safety concept. In turn, this system has been rolled it out to six Group companies in Japan and overseas. The final target safety level is set as a common target for all business sites (Safety Stage 3), regardless of the risk at the site.
In addition, the system makes it possible to analyze not only the entire business site but also by department and job type, enabling a better understanding of the strengths and weaknesses of each individual.
Since the results for 2023 were fed back to the relevant business sites, we plan to reflect them in the safety activities of each business site and monitor them regularly as a verification.
In 2024, we plan to expand the system to nine business sites in Japan and overseas, mainly at manufacturing sites.
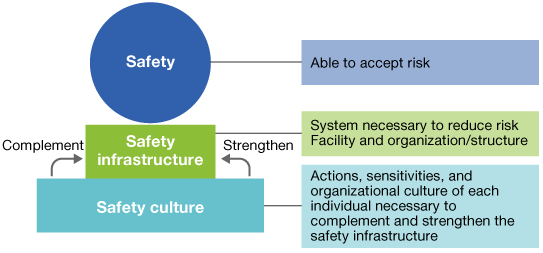
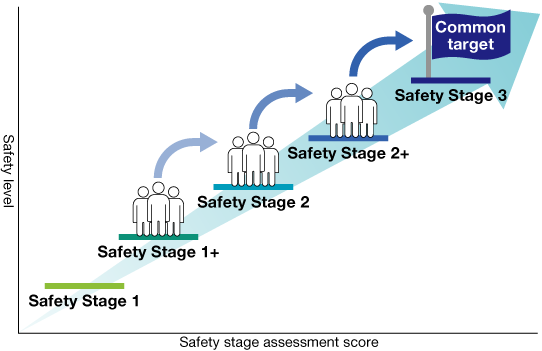
JSR Safety Day
In July 2014, a tragic accident occurred at JSR's Yokkaichi Plant that resulted in the loss of the life of a young colleague. We recognize that we must always remember the heartbreaking of that day and cherish the lessons learned. JSR Safety Day is an opportunity to reaffirm our determination to never allow such a tragic accident to occur again.
The 2023 JSR Safety Day was held on July 21 at the Yokkaichi Plant. In the first half of the ceremony, the president gave a lecture and we introduced our basic safety philosophy along with highlighted company-wide safety activities. In the second half, with the aim of raising the level of safety awareness and safety activities among employees, we expanded the scope of participation to include the Group and held a safety and health activity forum. Outstanding activity themes related to occupational safety, security and disaster prevention nominated by each business site were selected as the target themes of the forum through a rigorous examination.
This time, presentations were held on the following three themes, and there were lively opinions and questions from the audience. These presentations are streamed online after the event so that those who were unable to attend can watch.
- Initiatives to eliminate occupational accidents in research departments (JSR Tsukuba)
- Use of ICT cameras to eliminate unsafe behavior (JSR Yokkaichi)
- Risk reduction activities at TUM Ube Plant (TUM Ube)
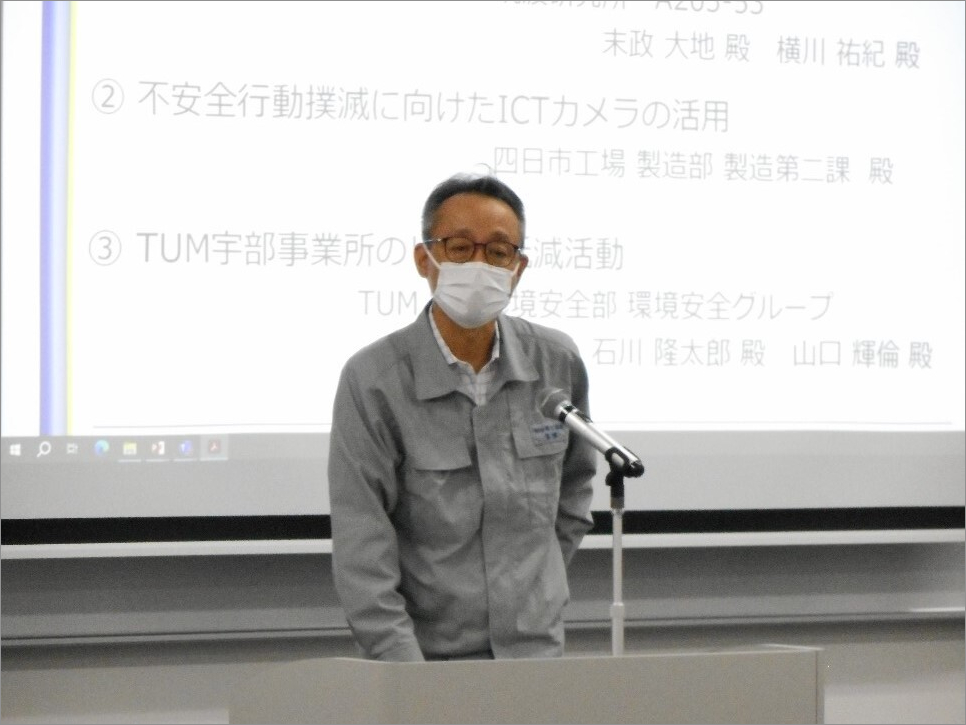
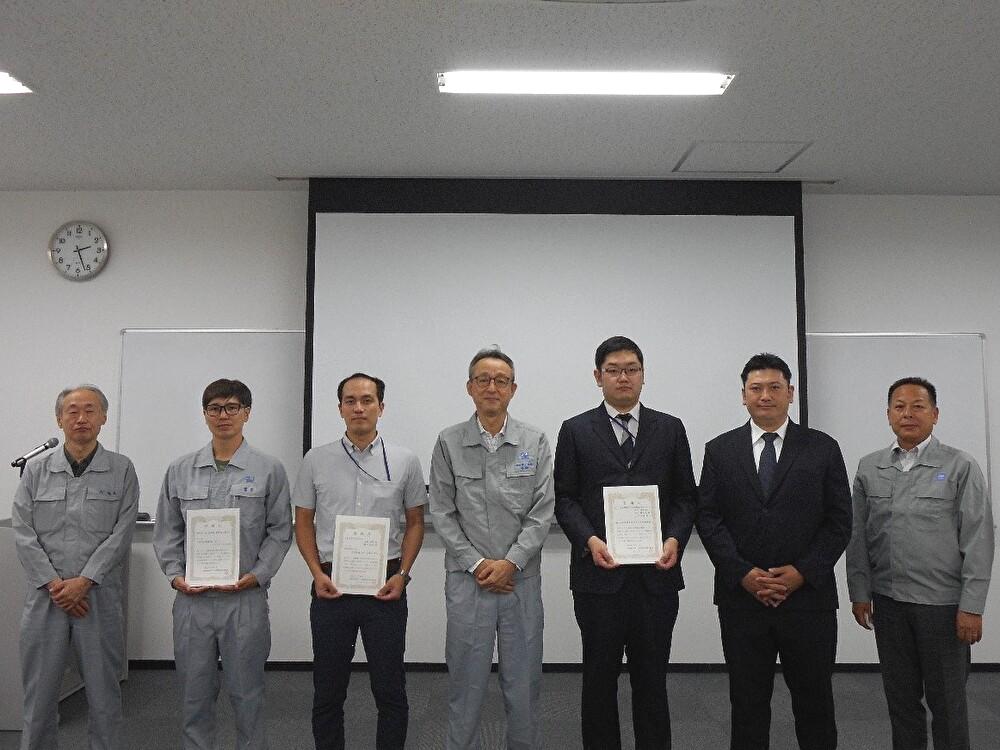
Environment and Safety Audit
An audit team of the Environment and Safety Department at JSR Headquarters conducts annual audits of JSR Group’s plants and laboratories on a regular basis. These audits are conducted according to an audit plan and check sheet*. They verify the effectiveness of the management system in place at each department based on the results of interviews and objective facts (evidence, on-site inspections, etc.) on the status of occupational safety, security, disaster prevention, environmental conservation, and chemical management.
In the effectiveness verification, areas for improvement are not only pointed out, but we also focus on the strengths of each department, and share the results obtained with each of the Group's business sites in an effort to improve the safety level of the entire Group.
Furthermore, the audits also provide an opportunity to share and discuss issues faced by audited departments, and the Group comes together to resolve issues in environmental and safety activities.
On the last day of the audits at JSR business sites, the President of JSR directly participates as a top auditor. In addition to reporting on the audit results, we strive to grasp the actual status of environmental and safety activities at the relevant sites through reports on activities at the sites, dialogue meetings between top management and employees, and on-site inspections.
* Prepared based on the Risk-Based Process Safety (RBPS) approach
In FY2023, we expanded the scope of audits not only to Japan but also to the Group overseas in Asia. In addition to risk management, legal compliance management, and accident management, the audit also confirmed the instillment of JSR Group's shared safety concept, which is one of the activities to foster a safety culture. No urgent issues were found at any of the business sites audited.
In addition, structural improvements associated with the company split were a major issue in the previous fiscal year, but we confirmed that substantial improvements have been made. For individual issues, we ask each business site to make improvements in a way that is satisfactory. We plan to check the status of improvement in the next audit.
Scope of FY2023 Headquarters Environment and Safety Audits
JSR Corporation (3 business sites)
Yokkaichi Plant & Research Laboratories
Tsukuba Research Laboratories / Tsukuba Site
JSR-Keio University Medical and Chemical Innovation Center (JKiC)
Domestic group companies (8)
JSR ARTON Manufacturing Co., Ltd.
JSR Micro Kyushu Corporation
JSR Life Sciences Corporation
UJK Co., Ltd. Yamaguchi Plant
Medical & Biological Laboratories Co., Ltd. (Tsukuba Laboratory)
Emulsion Technology Co., Ltd.
Techno-UMG Co., Ltd. (Yokkaichi Plant, Ube Plant)
Japan Coloring Co., Ltd.
Overseas Group Companies (3)
JSR Micro Korea Co., Ltd.
JSR Micro (Changshu) Co., Ltd.
JSR (Shanghai) Co., Ltd. (Shanghai Technical Center)
Internal and External Communication
Activities to Reduce Number of Occupational Accidents at Contractors
JSR has established the Comprehensive Disaster Prevention Committee (CDPC) for communication with its contractors that perform various work and construction at each business site. When our contractors notice something in their operations or identify areas that need improvement, we ask them to share this information at the CDPC and set up opportunities for communication as necessary. We then share opinions to ensure safety and advance operational improvements.
If an accident or disaster occurs in the operations handled by a contractor, we work with that contractor to investigate the root cause, implement countermeasures, and verify their effectiveness to prevent a recurrence. Not only do we share this information within the Group, but we also share it with contractors as necessary to prevent accidents.
We strive to ensure the safety of all employees working at JSR by collaborating with other companies to advance occupational safety activities.
Example Safety Activities Conducted by CDPC
Name | Details |
---|---|
Safety training for member companies | Training on occupational accidents through case studies, experience-based training, and risk prediction is provided to safety instructors of member companies to improve their knowledge, skills, and sensitivities toward safety. |
Special patrol for regular maintenance | Members of the Comprehensive Disaster Prevention Committee conduct patrols during regular maintenance periods to identify and eliminate unsafe elements that may emerge or materialize from a third-party perspective. |
Communication with Communities and Society
JSR is a member of the Japan Chemical Industry Association, Japan Petrochemical Industry Association, the Japan Society for Safety Engineering, and the Japan Industrial Safety Competency Center. Through the following safety activities and our Responsible Care program, we communicate with communities, society, and peer companies, sharing information both in Japan and abroad.
- Hosting of or participation in accident prevention training drills of firefighting authorities and joint training with other nearby companies
- Participation in joint accident prevention organizations with nearby companies
- Participation in disaster prevention councils in the community
- Participation in local dialogue on Responsible Care
- Response to CSR surveys from other companies/organizations
The Group’s business sites in Japan and overseas also actively communicate with their local communities to increase awareness of safety, improve safety technologies, and reciprocally prevent accidents. Each of the Group's business sites, including those overseas, actively communicates with the communities in which they are located to improve mutual awareness and technology related to disaster prevention and safety.
4. Training
Occupational Safety, Security and Accident Prevention Training
JSR conducts on-the-job training (OJT) at each business site and offers experience-based, practical skills training in miniature plant setting at its company-owned and operated training centers. This training helps to instill knowledge, skills and sensitivity to security management
Training on work processes includes an experience-based component provided in a virtual space using virtual reality (VR). Through experiencing fear that is difficult to replicate in real life for safety reasons, employees are able to increase their safety awareness and make efforts to eliminate unsafe actions.
In addition to mandatory training under Industrial Safety and Health Act, we provide training on occupational safety, security and accident prevention in rank-based training for each job type in stages. In addition to gathering opinions on the training from the top management and frontline workers of the business sites, we survey the participants and instructors after the training and use the results to continuously review the curriculum and approaches.
The main training conducted in FY2023 is shown in the table below.
Item | Summary | Method | Target | Number of participants | Total number of training hours |
---|---|---|---|---|---|
Training for new employees |
Learn the basic rules of the company and the business site to which the participant belongs. In the safety part, recognize the safety philosophy and understand the approach to and importance of safety. |
Group education | JSR Corporation | 82 | 7734.5 |
Common skills education for plants |
Acquire specialized knowledge of safety and manufacturing processes (introduction, beginner, intermediate, and advanced). In the introduction, participants receive experience-based training in getting caught in machinery, falling, and electrostatic dust explosions to understand the importance of safety through practical training. |
Group education e-learning |
JSR Corporation | 244 | 3441 |
Group companies in Japan | 45 | 581.25 | |||
Miniature plant training | In addition to plant startup, which cannot easily be experienced at the actual plant, participants learn how to discover and deal with tripped circuits and other abnormalities and loss of control through practical training. | Group education | JSR Corporation | 53 | 148.25 |
Group companies in Japan | 11 | 31.75 | |||
Management skills training Safety management |
Training of human resources who will play a central role in improving and advancing workplace safety activities by learning how to prevent accidents and implement effective roll-out using examples of facility accidents. | Group education | JSR Corporation | 5 | 69.75 |
Emergency Response
The Group established the Risk Management Regulations to identify and mitigate important risks such as fires and explosions, environmental accidents, serious occupational accidents, and serious natural disasters. In addition to matters related to risk management, the regulations also describe communication methods in the event of an emergency and how to prevent the spread of damage. The regulations are used throughout the Group, including overseas.
In 2023, we established a task force at JSR Headquarters and reviewed the method of communication in the event of an emergency. JSR Headquarters departments in charge and each business site conducted tests to coordinate communication routes and reporting details, and confirmed that they could respond without any problems. Going forward, we will continue to conduct individual and company-wide emergency response drills with each business site to prevent the spread of damage in the event of an emergency.