Providing Value to Society through Our Business Activities
Contribution to Preservation of the Global EnvironmentDeveloping Products That Reduce the Environmental Impact of Our Customers
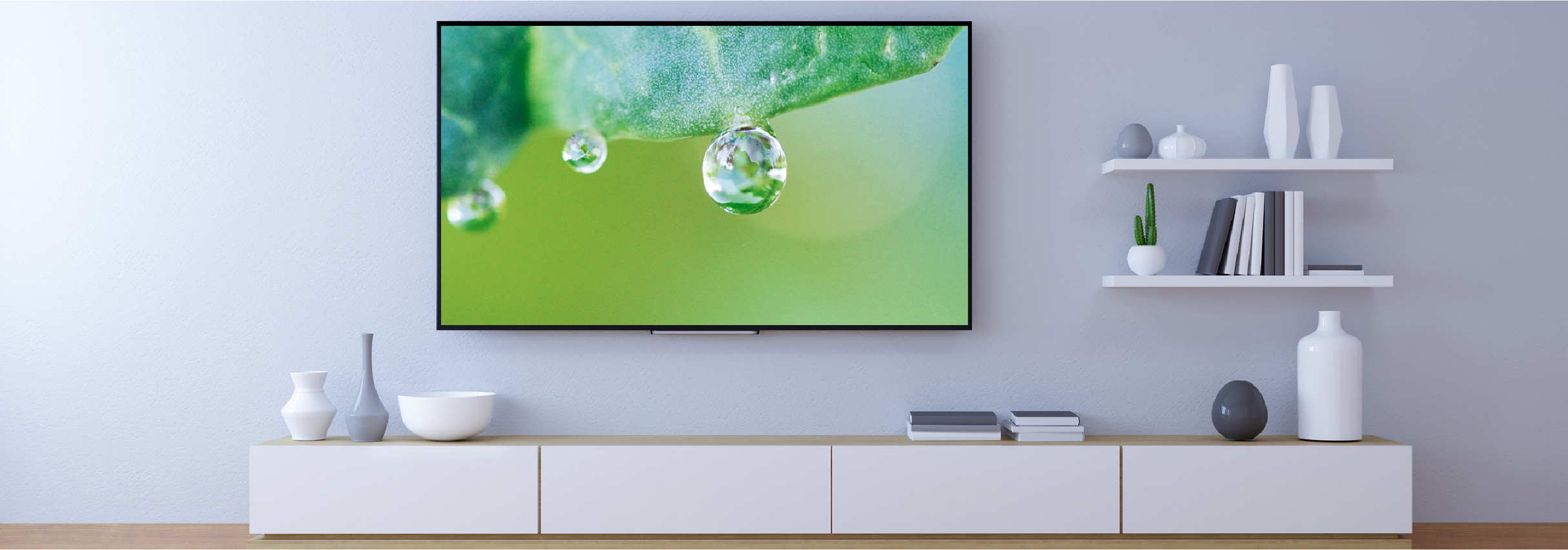
Contributing to Energy and Resource
Saving with Display Materials
Lowering the Firing Temperature with Low-temperature Materials Reducing Energy Consumption in the Manufacturing Process
Conventionally, the technological development of liquid crystal display materials was focused on the aim of reducing power consumption of the display panel itself such as by improving luminance (brightness) and the display response speed. However, we have been working on the development of a low-temperature material aiming to reduce the environmental impact in the manufacturing process of display panels.
The low-temperature material we have developed allows the conventional firing temperature of 230°C to be lowered to 150°C. The material is designed to have the same performance as before. Accordingly, using this material leads to an approximately 10% reduction in energy consumption in display panel manufacturing. We will strive to further spread this low-temperature material in the future to contribute to building an even richer society and reducing power consumption.
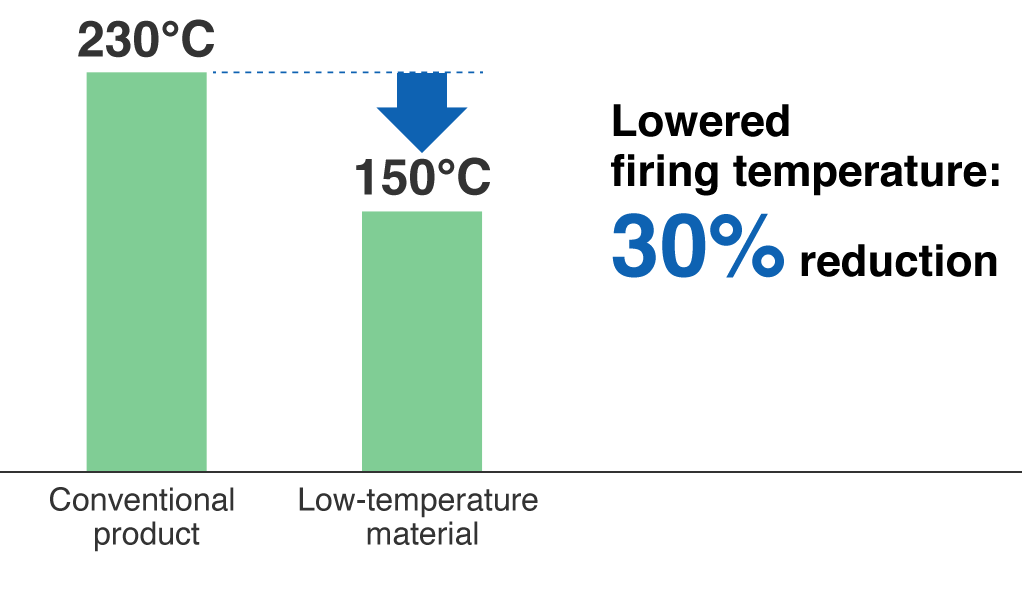
Launch of an Alignment Film Recycling Business
Alignment film is one of the important materials used to control liquid crystal behavior in liquid crystal displays. We have supported the progress of liquid crystal displays as a leading company in the development and sale of alignment films over many years.
Leftover chemical material and used waste liquid is generated in the process of forming alignment films for displays. There is a risk that material and liquid will leak during transportation or storage. In addition, great care must also be taken in handling when disposing of them. Accordingly, we have launched an alignment film recycling business to support our customers in efficiently using materials and to reduce their environmental impact. We will work to reduce the environmental impact and improve customer satisfaction by widely providing materials we have recycled based on the extensive knowledge in alignment films we have accumulated over time.
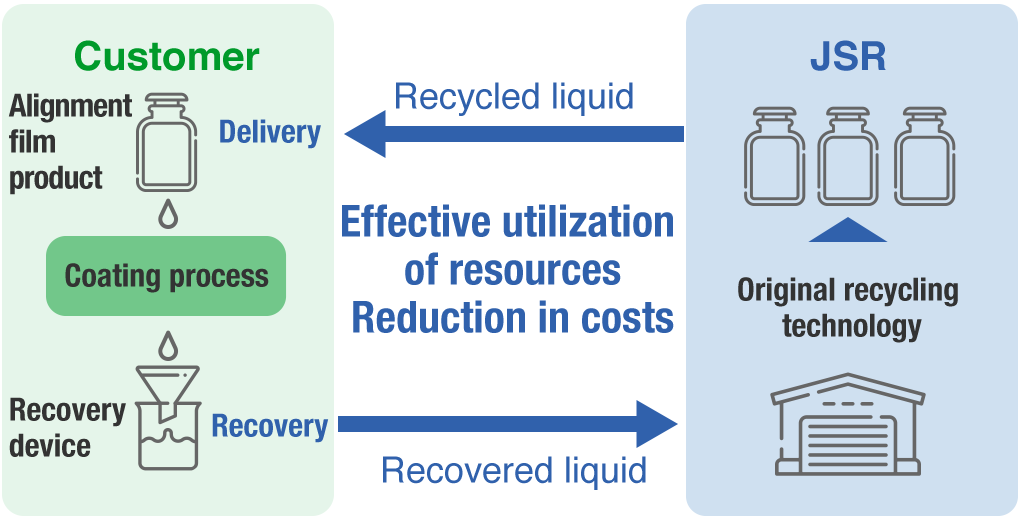
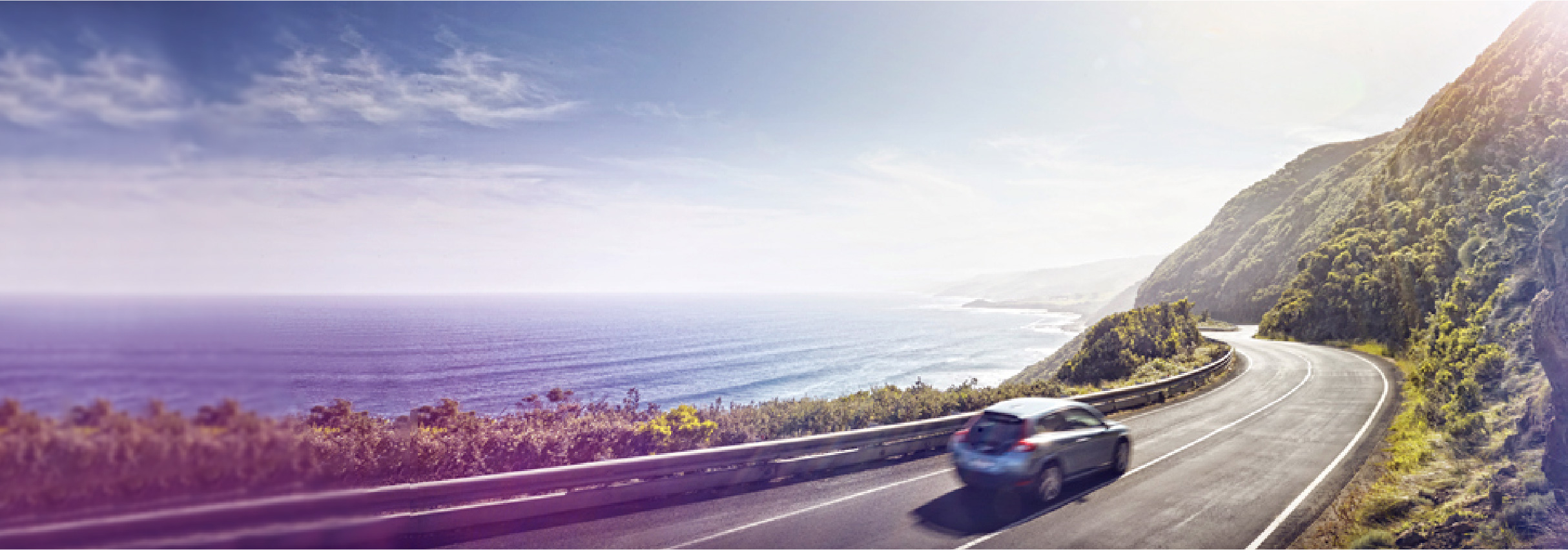
Toward Automobile Plastic Material
Resource Circulation
Aiming to Eliminate Painting and Promoting the Recycling of Automobile Parts with VIVILLOY®
VIVILLOY® highly colorable and highly weather resistant materials are materials which express high color development even without painting. We developed these materials based on our unique polymer development technologies we have cultivated through our track record in the global sale and supply over many years of weather-resistant materials (DIALAC® series) and alloy products (composite materials with other resins).
VIVILLOY® also contributes to energy saving and an improvement in work efficiency in addition to cutting costs with the omission of the painting process. Moreover, JSR Group is implementing the closed recycling of plastic parts with the cooperation of our customers in office automation equipment applications. We will utilize this knowledge to also consider the recycling of unpainted parts of automobiles.
Recycling Process
Application Examples
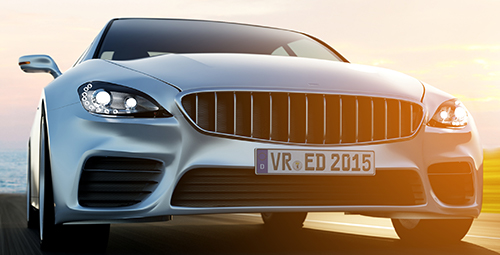
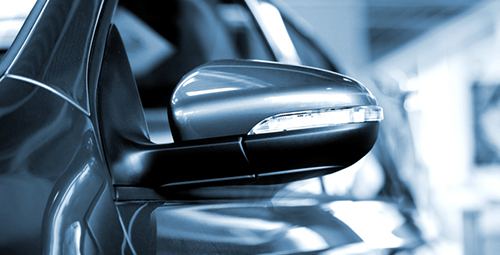
Utilizing Paintless Applications to Reduce GHG Emissions by over 40% and Contribute to Environmental Conservation with Highly Recyclable Parts
Materials used in automotive exterior parts, such as plastics and ABS resin, undergo secondary processing such as plating and painting to maintain their aesthetics and functionality even in harsh environments. However, this process is very costly and also emits a large amount of GHG emissions.
VIVILLOY® helps to solve these problems. In addition to the excellent weather resistance and scratch resistance required for exterior parts, the coloring is comparable to that of painting, which eliminates the need for secondary processing. Therefore, switching materials to VIVILLOY® can reduce costs by about 30% and GHG emissions by more than 40%. Furthermore, when recycling materials, conventional products require paint stripping, a process that VIVILLOY® does not require. Moreover, VIVILLOY® is exceptionally durable, retains the same performance as virgin material even after long-term use, and has been proven to offer excellent recyclability.
With these features, we are developing a system to accelerate VIVILLOY®’s adoption and have it recognized as a paintless highly colorable material not only for use in the automotive sector but also in a wide range of other fields such as office automation equipment. Our research laboratory is reviewing the polymer design and developing a new product with even greater coloring, which is scheduled to be launched in FY2024. Going forward, we will carefully examine the needs and market potential of new applications such as EVs and autonomous driving, and not only strengthen VIVILLOY®'s performance, but also develop new high-performance products and build a stable supply system. Furthermore, by strengthening cooperation with overseas subsidiaries and expanding this business overseas, we hope to contribute widely and deeply to global environmental conservation.
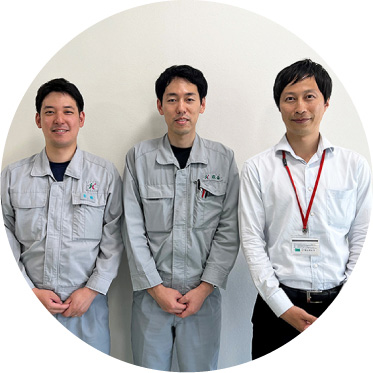
H.A.R&D Headquarters
Techno-UMG Co., Ltd.
K.H.R&D Headquarters
Techno-UMG Co., Ltd.
Y.S.Sales and marketing headquaters
Techno-UMG Co., Ltd.
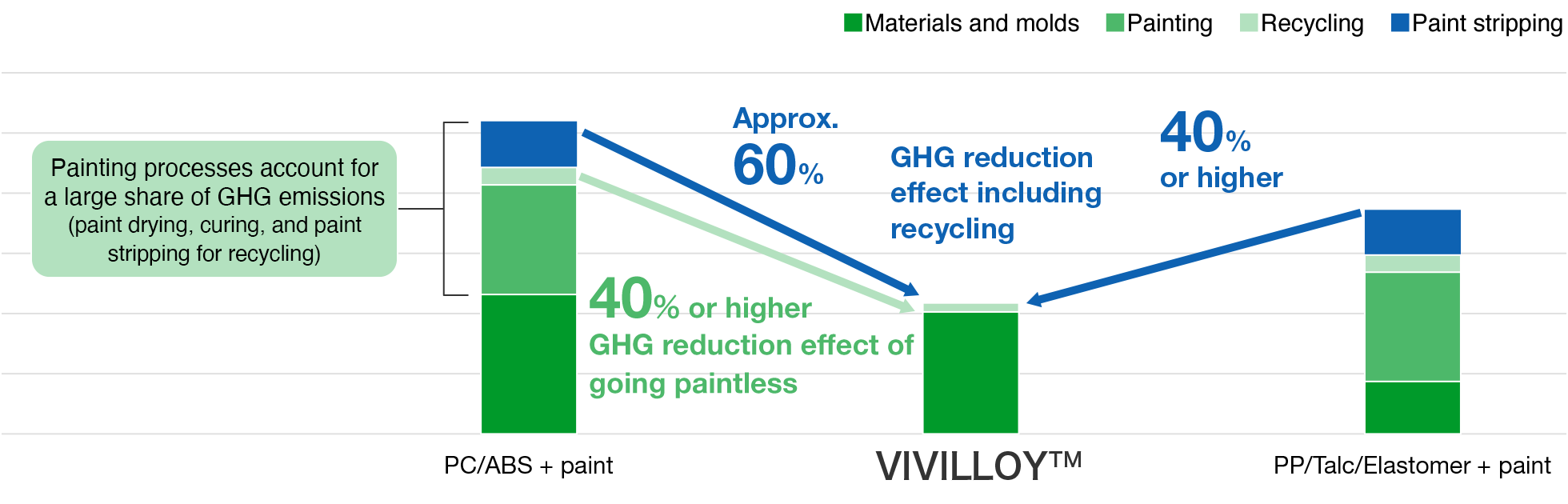
* GHG emission intensity quoted from databases is used to cal-culate GHG reduction effects.