- 1. Philosophy and Course of Action for Occupational Health and Safety,
Policy for Security Management - 2. Advancement Structure and Management System
- 3. Medium-Term Plan for Health & Safety and Security Management
- 4. Occupational Health and Safety Initiatives
- (1) Numerical Targets and Priority Activities
- (2) Workplace Accident Record
- (3) Activities in FY2018
- (4) Looking to FY2019
- 5. Security Management Measures
- (1) Numerical Targets and Priority Activities
- (2) Facility Accident Record
- (3) Activities in FY2018
- (4) Looking to FY2019
- 6. Activities Common to Occupational Health and Safety and Security Management
- (1) Health & Safety and Security Management Education
- (2) Organization and Education for Safe Plant Operation
- (3) Safety Ceremony and Safety and Health Activity Forum
- (4) Safety Competency Assessments by the Japan Safety Competency Center
1. Philosophy and Course of Action for Occupational Health and Safety
JSR has established a “Course of Action for the Philosophy for Occupational Health and Safety” that present specific actions demanded of the company and each of its employees. It is based the “Philosophy For Occupational Health and Safety” that is spelled out in the “Top Commitment” issued by JSR’s top management and which serves as the basis for realizing worksites in which everyone can work “healthily,” “safely,” and “with peace of mind.”
Philosophy for Occupational Health and Safety
At JSR Corporation, safety is our highest priority and the foundation of all of our activities.
Accordingly, we will create safe worksites and strive to maintain physical and mental health, with the goal of ensuring a safe return home at the end of each workday.
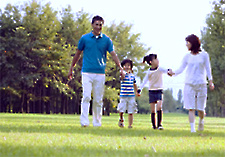
Courses of Action of the Philosophy for Occupational Health and Safety
- No matter the situation, we will act with safety foremost in mind.
- We will comply with established rules and never fail to act in accordance with safety basics.
- We will maintain safety by identifying and eliminating both actual and potential hazards.
- We will strive to create comfortable work environments and promote physical and mental health.
- Through communication and ingenuity, we will aim to achieve 100% employee participation in all safety activities.
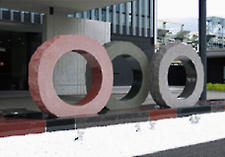
In addition, we use the “Philosophy for Occupational Health” and “Course of Action for the Philosophy for Occupational Health and Safety” as the basis for establishing health and safety policies in our plants that are matched to the individual characteristics of each plant in terms of its organizational makeup, workplace environments, and other traits.
Health & Safety Policy for the JSR Yokkaichi Plant
Health & Safety Policy for the JSR Chiba Plant
Health & Safety Policy for the JSR Kashima Plant
Policy for Security Management
JSR establishes a “Policy for Security Management” that presents the company’s aim to be an accident-free organization, one in which all employees practice autonomous and proactive safety activities by accepting the “Philosophy for Occupational Health” and “Course of Action for the Philosophy for Occupational Health and Safety.”
Policy for Security Management
(1) Extremely Safe Behavior
The Philosophy for Occupational Health and Safety has penetrated through the organization, the Course of Action are established as applying to everyone, and safety competency is improving through independent safety activities.
(2) Enhanced Human Resources and Organizational Strength
High personal skills, organizational ability, and a healthy organizational culture are being maintained with the establishment and execution of the education and training programs needed for organizational management.
(3) Optimal Risk Management and Security Measures
Security measures corresponding to risk importance are being efficiently and effectively implemented using new technologies.
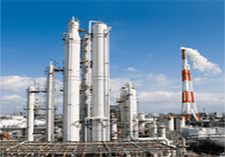
2. Advancement Structure and Management System
Activity policies and action plans concerning JSR Group’s occupational health and safety, security management, and other matters are deliberated and formulated by the Responsible Care (RC) Promotion Committee, which is chaired by the officer in charge of safety and environmental affairs. The RC Committee also oversees the results of those activities.
Occupational Health and Safety Management System and Audits of Headquarters Environment and Safety
JSR has developed and operates an “Occupational Health and Safety Management System” that establishes regulations and procedures concerning occupational health and safety and the prevention of accidents. Internal audits are conducted within JSR’s business establishments to confirm the effectiveness of this management system. Additionally, an auditing team led by the President conducts annual Safety and Environment Audits in plants and laboratories to verify the effectiveness of each business establishment’s health-and-safety and security-management activities that are based on the management system.
Labor-Management Health and Safety Committees
Once a month, each of the business establishments in JSR and domestic Group companies hold a labor-management health and safety committee meeting in accordance with the Industrial Safety and Health Act.
Representatives of both the company and employees attend the meetings. The labor side presents its views on important matters, such as measures to prevent hazards to workers and health problems (i.e., the causes of workplace accidents and measures to prevent their recurrence). Then both sides work together to prevent workplace accidents.
3. Medium-Term Plan for Health & Safety and Security Management
We have been comprehensively reexamining our safety activities and business establishments’ operations ever since a serious workplace accident in 2014. Using a two sided approach comprised of “safety infrastructure” (equipment, organization, and mechanisms) and “safety culture” (people and climate), we are striving to improve safety in our organization with recognition that “safety infrastructure” + “safety culture” = “safety competency.”
“Recreating the safety culture” is presented as a management issue in JSR’s medium-term plan. We therefore aim to develop human resources possessing strong awareness of safety and to create accident-free workplaces that are safe and secure.
JSR Roadmap for Health & Safety and Security Management
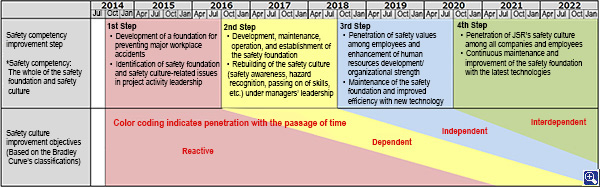
Notes:
Reactive: No action unless an accident happens; response by instinct
Dependent: Management by a supervisor/safety officer; doing what one is told to do
Independent: Action on a personal level; ability to act alone without being told
Interdependent: Working on colleagues; mutual awareness with colleagues)
(Source: DuPont)
4. Occupational Health and Safety Initiatives
(1) Numerical Targets and Priority Activities
Using the JSR Roadmap for Health & Safety and Security Management, we implement activities by establishing action plans comprised of annual targets, annual policies, and priority measures that take into account actual performance and activities of the previous fiscal year. In FY2018, we focused attention on “elimination of unsafe behaviors” and “Stratified safety education” with the aim of finishing the year to “Zero workplace accidents (lost time accidents).”
(2) Workplace Accident Record
No lost time accidents nor non-lost time accidents affecting JSR employees occurred in FY2018. Among our manufacturing partners, there were no lost time accidents; however, there was one lost time accident.
Number of Workplace Accidents
(JSR)
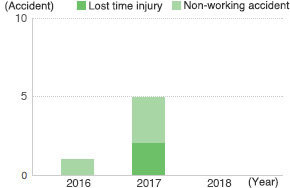
Number of Workplace Accidents
(Manufacturing Partners of JSR)
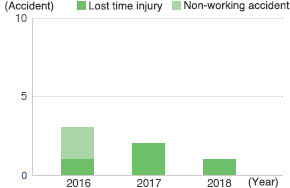
Among domestic Group companies, there were two lost time accidents and three non-lost time accidents in 2018. Among the manufacturing partners of domestic Group companies, there were no lost time accidents; however, there were two non-lost time accidents. Among domestic Group companies, an increasing trend is seen in terms of both the number of all workplace accidents and the number of lost time workplace accidents. Accidents involving tripping, falling, and entanglement are increasing.
Among overseas Group companies, workplace accidents continue to occur in a manner similar to that seen with domestic Group companies. We will make pertinent improvements by deepening collaborative safety activities throughout the entirety of JSR Group.
Number of Workplace Accidents
(Domestic Group Companies)
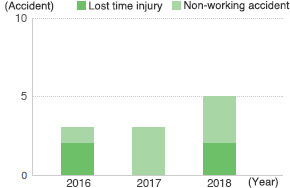
Number of Workplace Accidents
(Manufacturing Partners of Domestic Group Companies)
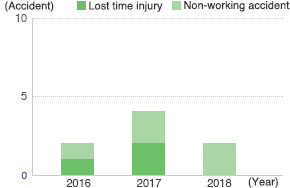
Information on workplace accidents that occurred at JSR Group is quickly and effectively communicated to all JSR employees and Group companies via the company intranet. This ensures that all of them share and understand the information, which helps prevent occurrence of similar accidents in the future.
(3) Activities in FY2018
Accident Prevention
Our activities in FY2018 focused on initiatives for improving hazard awareness while continuing efforts to penetrate “safety first” values among all employees. We promoted activities to eliminate unsafe behaviors that were matched to the circumstances of business establishments, which produced apparent effects in terms of employees’ notice of potential hazards. For this reason, we will present these activities to Group companies for implementation.
Although the number of workplace accidents is decreasing for JSR, such accidents continue to occur among Group companies. Within this trend, there is a continuous tendency whereby many accidents involve inexperienced young employees and veteran employees. We will therefore strive to realize accident-free workplaces by reinforcing efforts matched to the characteristics of each generation and by boosting collaborative safety activities between JSR and its manufacturing partners.
Promoting Education Matched to the Characteristics of Age Groups Prone to Workplace Accidents
We developed and began using curricula for hazard awareness skills improvement training that are designed for inexperienced young workers and physical limitations checks that are designed for veteran workers.
Hazard Awareness Skills Improvement Training for Young Workers | |
---|---|
Purpose | To improve hazard awareness skills by providing hazard awareness training based on understanding of the causes of workplace accidents |
Target | Young employees whose period of service with the company is between six months and one year |
Period | Underway since Jan. 2019 |
Content | Lecture → individual study → group exercise and discussion |
Assessment | Training effects (individuals): To be ascertained from the results of exercises and questionnaires |
Physical Limitations Checks for Veteran Employees | |
---|---|
Purpose | To encourage recognition of own situation by checking physical limitations that can lead to falling (questionnaire and measurement) |
Target | JSR employees, employees of a manufacturing partner, and other persons who are at least 50 years old, affiliated with an operations department, and work onsite |
Period | Between mid-November 2018 and the end of February 2019 |
Content | Pre-questionnaire (9 questions) Physical function measurements (5 items) |
Assessment | Five-stage evaluation of measured values |
(4) Looking to FY2019
We will aim to finish FY2019 with zero workplace accidents (i.e. lost time accidents).
To that end, we will strengthen our activity support and guidance for Group companies that had many workplace accidents and also continue our effort to eliminate unsafe behaviors. Moreover, we will work to prevent workplace accidents by expanding use of the curricula for stratified safety education that we began in FY2018.
Safety Initiatives of Comprehensive Disaster Prevention Councils
Within each plant of JSR and domestic Group companies, a Comprehensive Disaster Prevention Council (normally referred to as “Disaster Prevention Council) is set up with manufacturing partners that carry out construction and various operations in company facilities. The two sides team up to smoothly promote occupational health and safety activities.
Introduction of Disaster Prevention Councils’ Safety Activities
● Council-organized safety education
Disaster Prevention Councils provide group education to safety instructors of member companies using workplace accident case studies. They also provide hands-on safety education and hazard-prediction training (KYT).
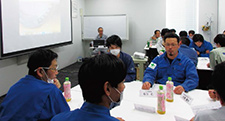
● Activities timed with National Safety Week
Disaster Prevention Councils raise safety awareness during National Safety Week by holding safety conferences, presenting safety activity reports prepared by subcommittees and member companies, and presenting awards for safety slogans. They also urge employees to engage in safe behavior by organizing active communication campaigns in the workplace.
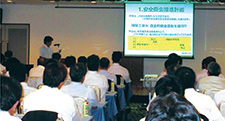
● Special patrols
Disaster Prevention Councils conduct “special patrols” led by council executives during periodic repair work.
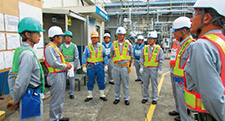
5. Security and Accident Prevention Initiatives
(1) Numerical Targets and Priority Activities
Based on the JSR Roadmap for Health & Safety and Security Management, we conducted safety inspections of our plants using HAZOP*1 and other methods to enhance our management of process accident risks and executed both infrastructure- and human-based countermeasures to important and major risks with the aim of finishing the year with “zero facility accidents (i.e. abnormal phenomena stipulated in the Act on the Prevention of Disaster in Petroleum Industrial Complexes and Other Petroleum Facilities) in FY2018.”
*1 Abbreviation of “Hazard and Operability Study.” It is a method of safety assessment used to identify hazards in processes and operations.
(2) Facility Accident Record
As listed below, the number of facility accidents at JSR in 2018 was two (both leaks) and the number at Group companies was four (one fire and three leaks). This information is reported to the government in compliance with the Act on the Prevention of Disaster in Petroleum Industrial Complexes and Other Petroleum Facilities. Holes caused by corrosion on pipelines were the main cause of the leaks. We are therefore putting priority on measures to address facility corrosion.
Number of Facility Accidents
(JSR)
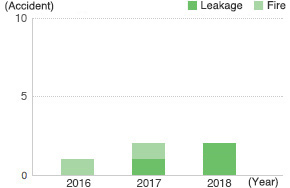
Number of Facility Accidents
(Group Companies)
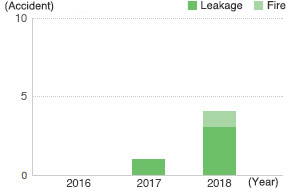
As with information on workplace accidents, information on facility accidents that occurred at JSR is quickly and effectively communicated to all employees via the company intranet. The information is also used in cause analyses, with the results being applied to education. Through these actions, JSR continues its effort to prevent occurrence of similar accidents in the future.
(3) Activities in FY 2018
Accident Prevention
Leakage accidents are increasing throughout JSR Group. Thus, measures against facility corrosion and deterioration have utmost importance at each business establishment. We are therefore checking the soundness of concerned facilities and making repairs with priority on those facilities having high risk in the event of a leakage. In addition, we began project activities aimed at eliminating leaks by reviewing our inspection and construction methods, with priority on pipe frame contact points.
We are working to prevent accidents by continuing to use HAZOP and implementing measures to address hazard risks that are uncovered and identified in our plants.
Preparations for Large Earthquakes
We adopted a mid-term business plan in FY1995 concerning preparations for a large earthquake and have been conducting systematic activities to enhance those preparations. Since FY2006, we have been doing seismic construction focused on high-pressure gas facilities in our plants based on the results of seismic performance assessments. We also installed earthquake early-warning systems at all JSR business establishments sites under the idea that “human lives first.”
Moreover, after the Great East Japan Earthquake prompted us to review the size of assumed earthquakes, we formulated safety measures that included enhancement of seismic resistance and tsunami countermeasures. We are currently implementing those measures systematically.
We will continue systematic seismic reinforcement work on spherical tank braces with an eye to completion in FY2020.
Yokkaichi Plant Administration Building
The Yokkaichi Plant Administration Building, completed in December of 2013, takes first-rate seismic measures. It can withstand earthquakes of up to 600 Gals using two types of seismic isolator: laminated rubber and oil dampers. In addition, a lattice structure ground improvement method was used to prevent liquefaction. This building has warehouses for disasters and ensures enough space to relocate headquarter functions in the event of a disaster in metropolitan Tokyo. The building also functions as the Yokkaichi City Tsunami Evacuation Building for local residents.
Yokkaichi Plant Clean Room Building C
Yokkaichi Plant Clean Room Building C, completed in July of 2014, incorporates advanced soil liquefaction prevention measures and a seismic isolation structure to ensure the stable operation of precision instruments. Valuable equipment is installed on higher floors to prevent damage from tsunamis.
(4) Looking to FY2019
We will aim to finish FY2019 with “zero facility accidents (abnormalities stipulated in the Act on the Prevention of Disaster in Petroleum Industrial Complexes and Other Petroleum Facilities).
We will systematically and steadily execute both infrastructure- and human-based measures to address important and serious risks, including natural disasters, to achieve this goal. We will also continue activities aimed at preventing accidents caused by aging equipment.
6. Common Activities of Occupational Health and Safety and Security Management
(1) Promotion of Risk Assessment
An important basis for process safety and workplace safety is risk assessment.
Using multiple risk assessment methods to ensure completeness, we identify serious risks and execute both infrastructure- and human-based countermeasures to deal with them.
Targets of Risk Assessment and Identification of Hazards
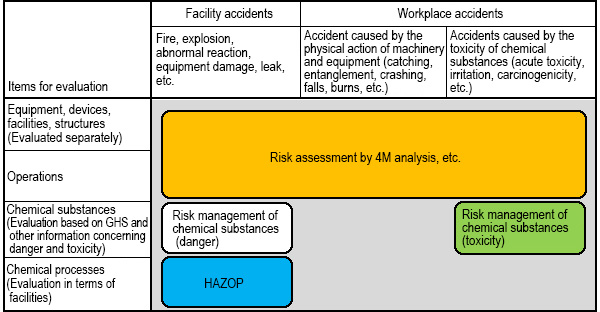
(2) Health & Safety and Security Management Education
JSR strives to improve employees’ knowledge, skills, and sensitivity by providing education on occupational health and safety in new employee training, mid-career employee training, and leadership training that is in addition to that legally required under the Industrial Safety and Health Act. Additionally, we improve knowledge, skills, and sensitivity pertaining to security management through hands-on safety and practical-skills courses in technical education and “miniature plant” training.
During FY2018, education on manufacturing skills common to all plants was provided 50 times at the Yokkaichi Training Center 50 times and attended by 593 employees. Additionally, “miniature plant” training was held at the same training center 6 times and attended by 75 employees.
(3) Organization and Education for Stable Plant Operation
Review of manufacturing-related organization and operations
In FY2017, we reviewed the necessary number of people in each manufacturing section and then divided organizations and expanded staffs so that managers can fully grasp their members. Workplace communication is improving as a result. We will continue ascertaining the effects of this organizational change and also look at how functions and roles are divided with other concerned departments.
Assessment of individual and organizational abilities
We have set desired levels for each rank of the job hierarchy and are striving to provide HR education that allows employees to reliably achieve those levels. We are also conducting assessments of individual employees' ability to operate specific equipment items and processes as well as their comprehensive abilities, and using them to maintain and improve organizational strength.
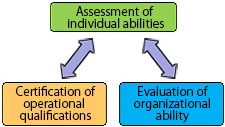
The Educational System (Conceptual Image)
(4) Safety Ceremony and Safety and Health Activity Forum
In FY2018, we held a Safety Ceremony and Safety and Health Activity Forum on July 19. The Safety and Health Activity Forum is an annual event in which we select presentation themes after carefully screening safety activities that were nominated by each business establishment. The following presentations were made in FY2018. After the presentations, a panel discussion was held by the presenters and became the scene of a lively discussion on ways of eliminating unsafe behaviors.
Presentation Themes of the FY2018 Safety and Health Activity Forum:
Presenting group | Title | Content |
---|---|---|
Kashima Plant Manufacturing Dept. | Verification of deviation in irregular operations through the “Sangen Shugi” principle | In hazard prediction using irregular worksheets, periodically reviewing irregular worksheets by young employees, veterans, and managers can help prevent troubles and accidents in irregular operations because it passes on “know-how” and “know-why” skills to young employees and improves their hazard awareness. |
Chiba Plant Manufacturing Technology Dept. | Reinforcing safety sensitivity: What do we need now? | As employees are rapidly becoming younger, we developed safety sensitivity, reinforced education, and focused on our own weak points identified from the results of a safety culture questionnaire.
|
Yokkaichi Plant Manufacturing Dept. | Improving safety management skills by utilizing ICT | We successfully improved safety management skills by utilizing tablet computers for daily inspection records and equipment management at manufacturing sites. Specifically, we used the tablets in 1) training on initial actions when a problem occurs (“what would you do?” training), 2) training for in-depth investigation of problems (troubleshooting meetings), and 3) development of safety indicators and signs. |
Yokkaichi Plant Manufacturing Dept. | Improving the Power Section’s emergency response abilities and creating a safety-conscious workplace environment | We implemented activities to improve the Power Section’s emergency response abilities and create a safety-conscious workplace environment. Specifically, we focused on 1) training on initial actions when a problem occurs (“what would you do?” training), 2) training for in-depth investigation of problems (trouble shooting meetings), and 3) development of safety indicators and signs. |
Yokkaichi Plant Manufacturing Dept. | Sharpening “ability to think” | In light of the many instances of human error (errors in judgment) that have occurred, we provided training in FY2017 to sharpen “ability to think” and thereby give employees the judgment skills needed to respond flexibly to unexpected safety situations. This training was in addition to traditional “thinking” education. Specifically, we focused on 1) hazard prediction training (KYT), 2) experience dealing with problems through actual equipment training, and 3) animating work standards. |
(5) Safety Competency Assessments by the Japan Safety Competency Center
The Kashima Plant, Chiba Plant, and Yokkaichi Plant received third-party “safety competency assessments” by the Japan Safety Competency Center. As a result of the assessments, it was confirmed that the Kashima Plant and Chiba Plant, which each underwent their second assessment, had improved in terms of both their safety infrastructure and safety culture compared to their assessments of four years ago. The assessments also identified areas in which each plant will need to make improvements. We will improve our safety competency by reflecting the assessments’ results on future activities.
We will address safety with renewed recognition that “safety is of utmost importance to everyone working in manufacturing and the bedrock of our business activities.”
JSR Group believes that safety is linked to the daily lives of all stakeholders and the bedrock of business activity. With this in mind, JSR Group has made it a goal to achieve zero facility accidents and zero accidents requiring time off from work. However, a serious workplace accident occurred at the Yokkaichi Plant in 23 July 2014.
With a pledge to aim for “zero accidents” and keep lessons learned from this serious workplace accident alive, and with a promise to continue developing a strong safety culture to protect precious lives, we erected a safety monument in front of the Yokkaichi Plant’s main building and also hold a safety ceremony as well as a forum for safety activities by business establishments each year at around the time of the accident.
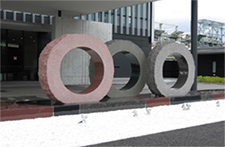
The safety monument