SocietyOccupational Health and Safety
1. Policy, Management System and Advancement Structure
2. Targets and Planning
3. Advancement of Risk Management (Occupational Health and Safety)
4. Compliance Confirmation and Certification
5. Education
6. Communication with Local Communities and Society
7. Activity Record
8. Handling of Emergency Situations (Facility Accident Incidence and Analysis)
9. Inspection and Monitoring
1. Policy, Management System and Advancement Structure
(1) Occupational Health and Safety Policy
Philosophy and Courses of Action for Occupational Health and Safety
JSR has established a “Course of Action for the Philosophy for Occupational Health and Safety” which presents specific actions demanded of the company and each of its employees. It is based on the “Philosophy for Occupational Health and Safety” that is spelled out in the “Top Commitment” issued by JSR’s top management and which serves as the basis for creating workplaces where everyone can work “healthily,” “safely,” and “with peace of mind.”
Refer to the link below on details on Philosophy for Occupational Health and Safety as well as the courses of action for Philosophy for Occupational Health and Safety.
(2) Safety Management System and Advancement Structure
JSR has developed and operates a “Safety Management System” that establishes regulations and procedures concerning security, accident prevention and occupational health and safety, all of which are based upon the “Security Management Manual” and “Occupational Health and Safety Manual / Health and Safety Manual” created in accordance with JSR’s security management regulations.
Internal audits are conducted within JSR’s business establishments to confirm the effectiveness of this management system. Additionally, an auditing team led by the president conducts annual Headquarters Environment and Safety Audits in plants and laboratories, and the heads of these plants and laboratories conduct annual management reviews, to verify the effectiveness of each site’s health-and-safety and security-management activities according to the management system.
Advancement Structure
Activity policies and action plans related to the JSR Group’s occupational health and safety, security and accident prevention, and other matters are deliberated and formulated by the Environmental Safety and Quality Committee, which is chaired by the officer in charge of environmental and safety affairs. This Committee also oversees the results of those activities. Please refer to the following link for more information about the Environmental Safety and Quality Committee.
2. Targets and Planning
(1) Medium-Term Plan for Health & Safety and Security Management
JSR uses a two-sided approach comprised of “safety infrastructure” (equipment, organizations, and mechanisms) and “safety culture” (people and climate) as safety activities at business sites, improving “safety infrastructure” + “safety culture” = “safety competency” to support organizational safety. Towards that end, we have established and put into effect the “JSR Roadmap for Health & Safety and Security Management,” which is a medium-term plan for activities which promote the “re-cultivation of safety culture” and the development of human resources possessing strong safety awareness, and development of safe and secure workplaces with no accidents or disasters. Please refer to the following link for more information.
(2) Plant Safety Policy
We use the “Philosophy for Occupational Health and Safety”, “Course of Action for the Philosophy for Occupational Health and Safety” and “Policy for Security Management” as the basis for establishing safety policies in each JST plant that are matched to the individual characteristics of each plant in terms of its organizational makeup, workplace environments, and other traits. Please refer to the following link for more information.
(3) Activity Targets
Using the “JSR Roadmap for Health & Safety and Security Management,” we implement activities by establishing action plans comprised of annual targets, annual policies, and priority measures that take into account actual performance and activities of the previous fiscal year. In FY2020, we focused attention on “promoting risk management”, “eradicating unsafe behaviors/conditions” and “cultivating safe human resources”, with the aim of finishing the year with “zero workplace accidents (lost time accidents).” We also strengthened the support we provide to Group companies for the safety activities.
(4) Action Plans
We establish and implement annual action plans at each JSR business site, based on their individual policies and targets. Please refer to the following link for more information.
3. Promotion of Risk Assessment (Occupational Health and Safety)
Risk management serves as the foundation for process safety and workplace safety, and an important part of risk management is risk assessment (risk identification and evaluation). With regard to workplace accidents, JSR identifies risks from a multifaceted and comprehensive manner, such as regarding facilities, work, accident cases, etc., based on MHLW’s “Guidelines for Risk Assessment”. The identified risks are prioritized according to their potential damage and rate of incidence, and countermeasures for each are developed and introduced into business site planning. In cases where a new and particularly large risk is identified, countermeasures are introduced on an expedited schedule to quickly mitigate the risk and ensure safety. Then, while reexamining optimization of judgment standards and operational rules, we make approaches rapidly in cases where new, serious risks are identified, and make efforts to mitigate risks and ensure safety.
4. Compliance Confirmation and Certification
(1) Compliance Confirmation
At every business site within the JSR Group, a department is assigned to handle legal and regulatory management, and it is the responsibility of these departments to identify applicable security management and occupational health and safety-related laws, regulations and ordinances, as well as standards and guidelines established for plants, and to then develop and implement procedures for raising awareness of these laws, etc., among employees and for ensuring ongoing compliance.
Please refer to the following link for more information about compliance confirmation.
(2) Certification Renewal
Please refer to the following link for more information about certification of JSR's three plants according to the High Pressure Gas Safety Act, Fire Service Act and Labor Standards Act.
5. Education
At JSR, we use hands-on safety and practical-skills courses in technical education, as well as “miniature plant” training, to improve security management-related knowledge, skills and sensitivity. We also work to improve employees’ knowledge, skills and sensitivity by providing education on health and safety as part of new employee training, mid-career employee training, and leadership training, which is in addition to that legally required under the Industrial Safety and Health Act.
In order to ensure the success of our education and training, we review the education and training structure, organize a safety education-related skill map and develop and maintain a safety education curriculum.
Please refer to the following link for more information.
6. Communication with Local Communities and Society
JSR is a member of the Japan Chemical Industry Association, Japan Petrochemical Industry Association, Japan Society for Safety Engineering and Japan Safety Competency Center, and we engage in information exchange and information sharing, both in Japan and overseas, via the following responsible care and safety activities.
- Hold information exchange meetings with administrative bodies
- Hold/participate in disaster drills involving the fire department and nearby companies
- Participate alongside nearby companies in cooperative disaster prevention organizations
- Participate in local Disaster Prevention Councils
- Participate in responsible care community dialogs
In addition, our business sites both in Japan and overseas pursue communication with their local communities in order to facilitate mutual improvement in disaster prevention and safety-related awareness and technology.
7. Activity Record
Safety Ceremony and Safety and Health Activity Forum
The JSR Group believes that safety is linked to the daily lives of all stakeholders and is also the bedrock of business activity for companies. With this in mind, the JSR Group has made it a goal to achieve “zero facility accidents” and “zero lost time accidents”. However, a serious workplace accident which claimed the life of an on-duty employee occurred at the JSR Yokkaichi Plant on July 23, 2014. With a pledge to aim for “zero accidents” and keep the lessons learned from this serious workplace accident alive, and with a promise to continue developing a strong safety culture into the future to protect precious lives, we erected a safety monument in front of the Yokkaichi Plant’s main building and also hold a safety ceremony as well as a forum for presenting case examples of safety activities by business sites each year at around the time of the accident.
In FY2020, we held our Safety Ceremony and Safety and Health Activity Forum online, due to the COVID-19 pandemic, on July 21. During the Safety Ceremony, a video message from Director Kawasaki was communicated, and at the Safety and Health Activity Forum, favorable presentation themes were selected from among safety activity cases that were nominated by JSR and each Group company both within and outside of Japan after undergoing a careful review. The presentation below was delivered in the form of slides with audio, and President Kawahashi’s comments were streamed as a video. Access to this website was made possible from the JSR Group companies, leading to many website visitors as compared to the past.
Safety Ceremony, Safety and Health Activity Forum Public Website (Partially)
Safety oath
Message from Director Kawasaki
Comments by President Kawahashi
FY2020 Safety and Health Activity Forum Presentation Themes
* The table is slidable aside.
Safety Initiatives of Comprehensive Disaster Prevention Councils
Within each plant of JSR and domestic Group companies, a Comprehensive Disaster Prevention Council (normally referred to as “Disaster Prevention Council) is set up with manufacturing partners that carry out construction and various operations in company facilities. The two sides team up to smoothly promote occupational health and safety activities.
Introduction of Disaster Prevention Councils’ Safety Activities
Council-organized safety education
Disaster Prevention Councils provide group education to safety instructors of member companies using workplace accident case studies. They also provide hands-on safety education and hazard-prediction training (KYT).
Activities timed with National Safety Week
Disaster Prevention Councils raise safety awareness during National Safety Week by holding safety conferences, presenting safety activity reports prepared by subcommittees and member companies, and presenting awards for safety slogans. They also urge employees to engage in safe behavior by organizing active communication campaigns in the workplace.
Special patrols
Disaster Prevention Councils conduct “special patrols” led by council executives during periodic repair work.
8. Handling of Emergency Situations (Workplace Accident Incidence)
At JSR and JSR Group companies, there is a decreasing trend in terms of both the number of all workplace accidents and the number of lost time accidents. However, on May 14, 2020, there was a fatal accident at the Yokkaichi Plant in which an employee from an affiliate company died while opening a storage tank a part of a legal inspection. We are taking this accident very seriously, through thoroughly enforcing compliance with safety standards in work and striving to prevent reoccurrence. To ensure that all employees of JSR, JSR Group companies and affiliate companies understand and comply with safety standards, we are reinforcing construction management such as by reliably communicating safety information and reexamining confirmation forms. We are working to promote linkage across the JSR Group as a whole and reduce work accidents.
Number of Workplace Accidents in FY2020
Fatal accidents | Serious workplace accidents | Lost-time accidents | Non-lost time accidents | ||
---|---|---|---|---|---|
JSR | Employees | 0 | 0 | 0 | 0 |
Manufacturing partner employees | 1 | 0 | 1 | 1 | |
JSR Group Companies in Japan | Employees | 0 | 0 | 1 | 2 |
Manufacturing partner employees | 0 | 0 | 1 | 2 |
Number of Workplace Accidents
(JSR)Number of Workplace Accidents
(Manufacturing Partners of JSR)
Frequency rate
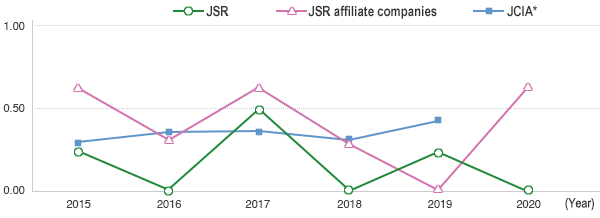
* Source: JCIA FY2021 Industrial Safety and Health Survey (data up to 2019 was recorded)
Number of Workplace Accidents
(Domestic Group Companies)Number of Workplace Accidents
(Manufacturing Partners of Domestic Group Companies)
Number of Workplace Accidents*
(Overseas Group Companies)
* Only accident numbers are listed, as the standards for workplace accident categories differ depending on the country of the accident location.
9. Inspection and Monitoring
JSR uses an auditing team led by the President to conduct annual Headquarters Environment and Safety Audits in plants and laboratories. From FY2015 onward, stimulation of environmental and safety activities has been promoted by changing to an auditing style which incorporates sharing and discussion of the audited departments’ issues and, on top of this, by establishing opportunities for dialog between top management and employees where both sides can share their thoughts with one another.
Please refer to the following link for more information.