Occupational Safety, Security and Accident Prevention
Message from the President
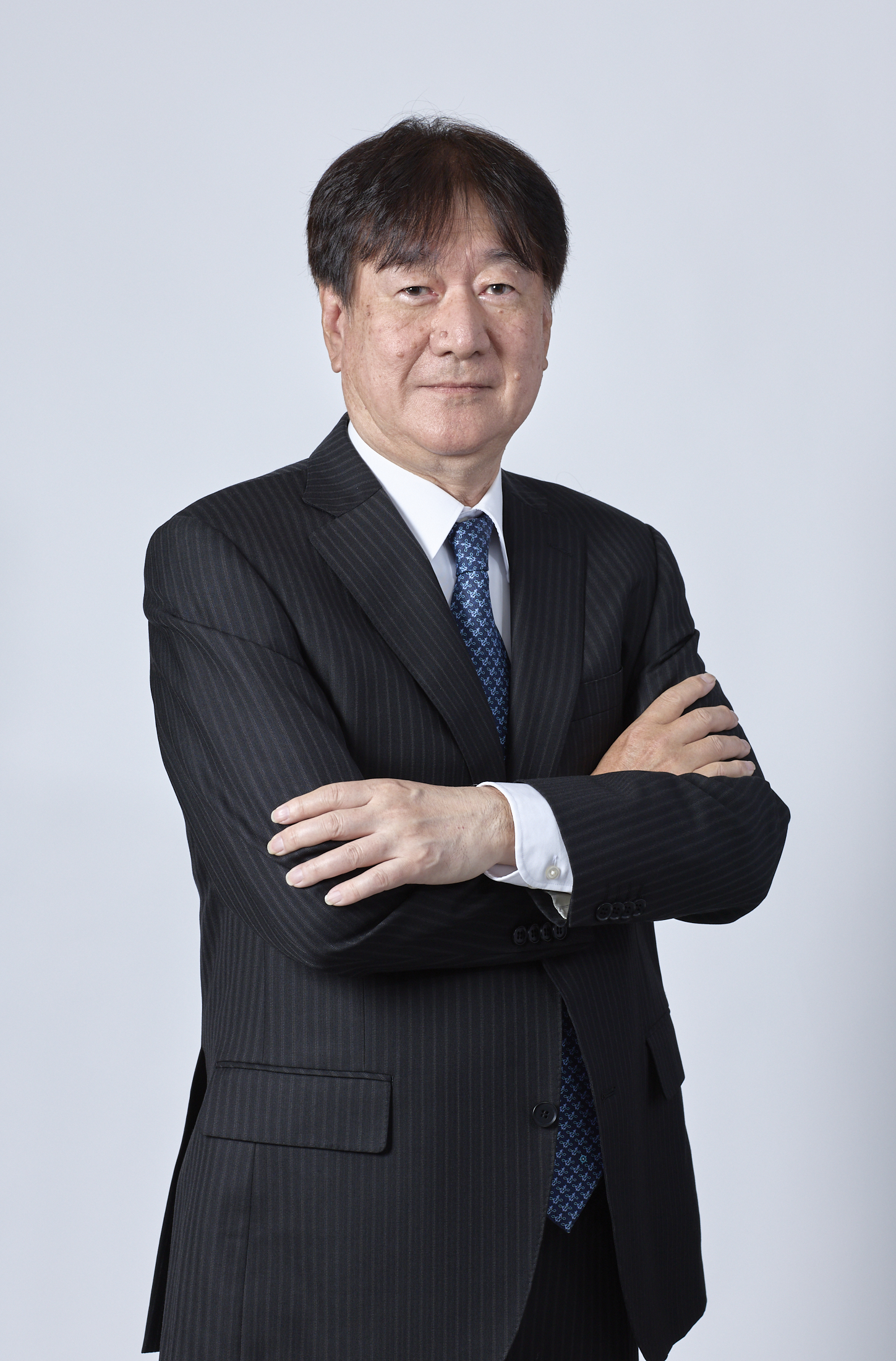
As a chemicals company, what is undeniably most important is safe and stable operations at our plants. Without this, we would not continue to be in existence.
Safety is the basis for business continuity, and is an investment for our company to grow. Safety is adopted as an important topic in management, and providing safety to local communities and developing our company into one where JSR Group employees and everyone working at our contractors are happy to work and maintain the status at are my responsibilities.
JSR completed the transfer of its elastomers business in April 2022. Today, we are working to achieve our business targets for FY2024 and establish a resilient management foundation. Safety is a particularly crucial element of these efforts. We must build a system that can withstand new environments and that is compatible with future business reforms.
To ensure that JSR continues to become a sustainable company trusted by society, top management is working with JSR Group employees toward developing a safety infrastructure and fostering safety culture so that we can further improve security and build human resources who are well-versed in safety.
Stay safe.
President and COO
Nobuo Kawahashi
1. Safety Philosophy, Management System and Advancement Structure
(1) Policy
JSR strives to prevent occupational accidents and facility-related accidents and promotes occupational safety, security and accident prevention measures to ensure safe and secure workplaces as well as the mental and physical health of its employees.
Philosophy for Safety
At JSR Corporation, safety is our highest priority and the foundation of all of our activities.
Accordingly, we will create safe worksites and strive to maintain physical and mental health, with the goal of ensuring workers happily take it for granted that they will return home safely at the end of each workday.

Safety Policy
- (1) Extremely Safe Behavior
- The Philosophy for Occupational Health and Safety has penetrated through the organization, the Course of Action are established as applying to everyone, and safety competency is improving through independent safety activities.
- (2) Enhanced Human Resources and Organizational Strength
- High personal skills, organizational ability, and a healthy organizational culture are being maintained with the establishment and execution of the education and training programs needed for organizational management.
- (3) Optimal Risk Management and Security Measures
- Security measures corresponding to risk importance are being efficiently and effectively implemented using new technologies.
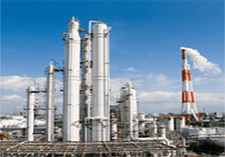
Courses of Action of Safety
- 1.No matter the situation, we will act with safety foremost in mind.
- 2.We will comply with established rules and never fail to act in accordance with safety basics.
- 3.We will maintain safety by identifying and eliminating both actual and potential hazards.
- 4.We will strive to create comfortable work environments and promote physical and mental health.
- 5.Through communication and ingenuity, we will aim to achieve 100% employee participation in all safety activities.
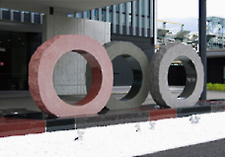
We post our philosophy and other pertinent information on our company intranet where it is easily accessible by employees to raise awareness on a daily basis. In addition, we utilize e-learning to conduct regular training for employees that increases the visibility of these policies and instills awareness.
We support the safety activities of Group companies following this philosophy.
(2) Safety Management System
JSR has developed and operates a “Safety Management System” based on the situation of each business site. This system establishes regulations and procedures concerning security, accident prevention and occupational safety, all of which are based upon JSR’s security management regulations.
To verify the effectiveness of this management system, we conduct Headquarters Environment and Safety Audits headed up by the CEO along with internal safety audits, safety patrols and management reviews regularly conducted every year by each business sites in an effort to achieve continuous improvement.
Furthermore, we have compiled manuals that contain appropriate and effective response measures that help to prevent damages from spreading in the event of an accident.
For the prevention of recurrences, all accidents are investigated to determine the cause so that proper countermeasures can be put into place and their effectiveness determined. In turn, we share this information within the Group to stop accidents before they occur.
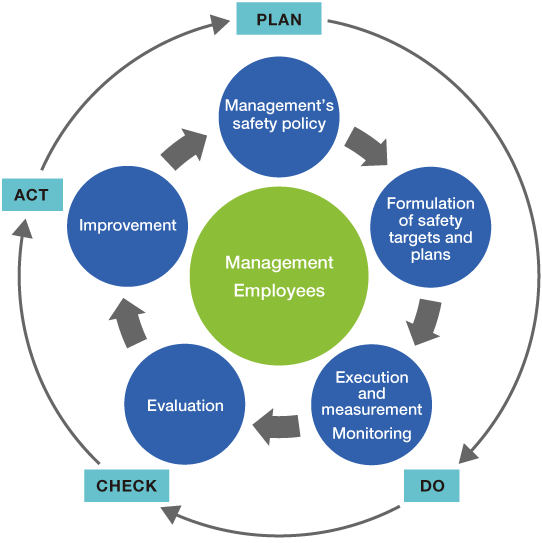
(3) Advancement Structure
JSR recognizes that safety is a cornerstone of business continuity and with this in mind we are implementing occupational safety, security and accident prevention efforts collectively as an organization.
JSR has put into place a powerful advancement structure headed up by the Environmental Safety and Quality Committee chaired by the officer in charge of environmental and safety affairs. Activity policies and action plans related to occupational safety, security and accident prevention are deliberated on and determined by this committee, based on the results of internal environmental and safety audits and management reviews.
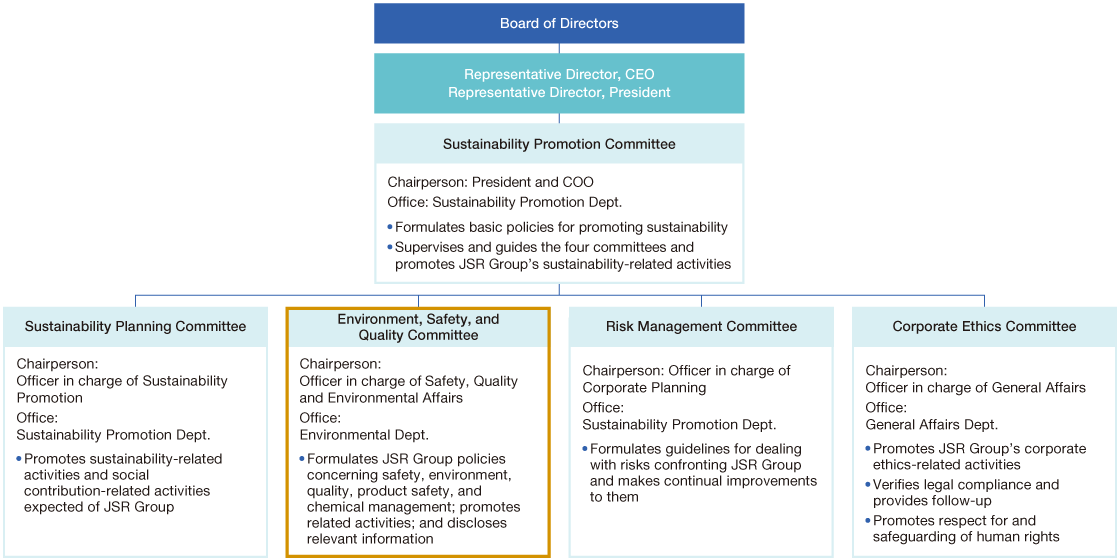
2. Targets and Planning
(1)Medium-Term Plan for Occupational Safety, Security and Accident Prevention
JSR aims to ensure safety in the workplace by conducting initiatives from the dual perspectives of fostering a safety culture (people and culture) and developing a safety infrastructure (facilities, organizations, and mechanisms) to improve security capabilities.
We formulated the JSR Occupational Safety, Security and Accident Prevention Roadmap as a medium-term plan in an effort to clarify the condition that each organization should strive for in terms of safety culture and safety infrastructure. The roadmap also covers the safety activities of each business site. The plan to become an Independent-type Organization by 2022 is somewhat delayed because the results of an employee survey indicate that we are still a Dependent-type Organization at present.
Going forward, JSR’s operating environment is expected to undergo substantial changes following the carving out of the elastomer business. Under our new corporate structure, we will steadily implement risk assessments and countermeasures in an effort to attain our targets.
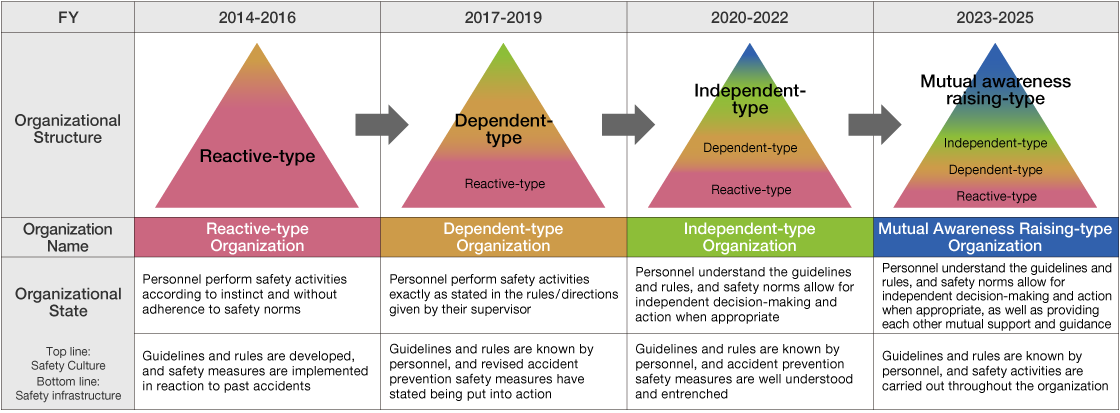
(2) Fiscal Year Targets and Plan
Under the JSR Occupational Safety, Security and Accident Prevention Roadmap, we have established targets and focal points of action plans for each fiscal year in light of the results of internal safety audits and management reviews conducted in the previous year. As a result, we are using a selection-and-concentration approach to implementing more efficient occupational safety, security and accident prevention efforts.
For FY2021, JSR has established the following targets and focal points.
Occupational safety | Security and accident prevention | |
---|---|---|
Targets | Zero occupational accidents*1 | Zero facility-related accidents*2 |
Focal points |
|
|
*1 Occupational accidents involving lost time
*2 Facility-related accidents corresponding to abnormal phenomena per the Act on the Prevention of Disaster in Petroleum Industrial Complexes and Other Petroleum Facilities
*3 RBPS stands for risk-based performance standards. A system for practical safety management of chemical plants issued by the Center for Chemical Process Safety (CCPS) of the United States in 2007.
3. Activity Record
Occupational Safety
FY2021 Occupational Safety Target: Zero Occupational Accidents (Lost Time)
As a member of Japan Petrochemical Industry Association and Japan Chemical Industry Association, JSR reports the number of occupational accidents to each organization.
In FY2021, there was one occupational injury involving lost work time at JSR and four at Group companies, for a total of five Groupwide, which fell short of our target. Looking back on the previous three years, the number of lost time accidents at JSR and its Group companies in Japan have been on the rise. Although not shown here, figures including no lost time accidents are also on the rise.
As a measure to eliminate occupational accidents, in response to the fatal accident involving an employee of a contractor that occurred in FY2020, we investigated the status of construction safety management at JSR and JSR Group companies and initiated improvements. Although we have not yet confirmed the effects, we will continue to strengthen our construction management system and promote the assurance of safety in construction works. For details of the activities, please refer to "(2) Reduction of Occupational Accidents at Group Companies and contractors."
Going forward, to ensure that all employees of JSR, JSR Group and its contractors understand and comply with safety standards, we will convey accurate safety information, review confirmation forms, and strengthen construction management. We will also deepen collaboration across JSR Group in an effort to reduce occupational accidents.
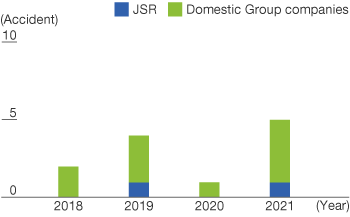
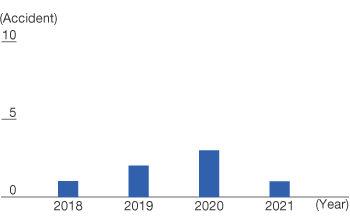
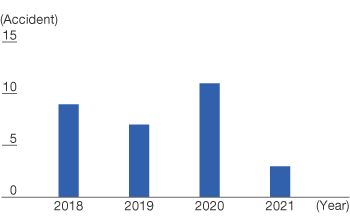
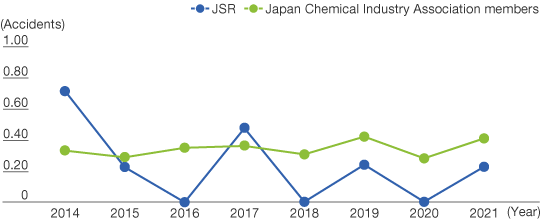
(1) Activities to Raise Safety Awareness
JSR strives to improve safety awareness and eliminate unsafe actions by fostering a safety culture with its training on occupational safety, including experience-based learning, security and accident prevention, risk assessment, and e-learning.
For activity records in FY2021, please refer to “5. Training.”
(2) Reducing Occupational Accidents at Group Companies and Contractors
Group Companies
JSR assesses the construction management system at its Group companies to prevent construction work related accidents. Through the assessment, we are providing feedback for improvement of risk identification and sharing of information. The assessment was performed at ELASTOMIX CO., LTD., JAPAN COLORING CO., LTD., and Emulsion Technology, Co., Ltd. in FY2021.
The change in business environment resulting from the split of our elastomer business is expected to also have an impact on our Group companies. Going forward, we will promote safety activities across the entire Group to further ensure safety.
Contractors
JSR has established the Comprehensive Disaster Prevention Committee (CDPC) with its contractors that perform various work and construction at each business site in order to improve communication. We strive to ensure the safety of all employees working at JSR by collaborating with other companies to promote occupational safety activities.
Name | Details |
---|---|
Safety training for member companies | Training on occupational accidents through case studies, experience-based training and risk prediction is provided to safety instructors of member companies to improve their knowledge, skills and sensitivities towards safety. |
Special patrol for regular maintenance | Members of the Comprehensive Disaster Prevention Committee conduct patrols during regular maintenance periods to identify and eliminate unsafe elements that may emerge or materialize from a third-party perspective. |
Security and Accident Prevention
FY2021 Security and Accident Prevention Target: Zero Facility Accidents (abnormal phenomena per the Act on the Prevention of Disaster in Petroleum Industrial Complexes and Other Petroleum Facilities)
JSR reports to administrative authorities on the number of facility accidents in accordance with the Act on the Prevention of Disaster in Petroleum Industrial Complexes and Other Petroleum Facilities.
In FY2021, there was only one facility accident (abnormal phenomena stipulated in the Act on the Prevention of Disaster in Petroleum Industrial Complexes and Other Petroleum Facilities) reported at a Group company, and none at JSR. Comparing the records from the past three years, this number of accidents has decreased. We believe our ongoing measures against age-related facility corrosion has yielded positive results.
As these measures have proven to be effective to some extent in enhancing facilities management, we are considering continuing them while also bringing other Group companies onboard going forward.
Upon analyzing minor issues that did not become accidents, we discovered that they were mainly attributed to work management such as poor construction, while there is an increasing rate of occurrence across the entire Group in recent years.
To address this, we plan to ensure thorough construction work management by expanding our support to contractors that conduct the work onsite to prevent future accidents.
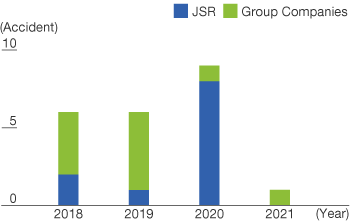
(minor issues included)
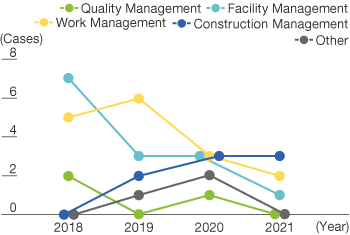
(1) Risk Management Implementation and Advancement
At JSR, we strive to conduct more effective risk assessment, which is considered the most important part of risk management.
In FY2021, we verified that risk assessment was systematically conducted at all business sites. In addition, we provided implementation training on HAZOP*1, which aims to optimize risk assessment for process safety, with the additional approaches of LOPA*2 and ALARP*3, and launched its operations.
Following the transfer of the elastomer business, the breakdown of business risks is also expected to shift. As such, we will continue to choose and utilize the assessment protocols appropriate for the risks in conducting risk management.
*1 HAZOP: An acronym for “Hazard and Operability Study.” It is a method of safety assessment used to identify the sources of hazards in processes and operations.
*2 LOPA: An acronym for “Layers of Protection Analysis”. It is a semi-quantitative method of evaluating the frequency of occurrence (probability of occurrence).
*3 ALARP: An acronym for “As Low As Reasonably Practicable”. It is a principle that states risks should be minimized as much as possible so long as the cost is justified with consideration for the efforts and costs necessary to reduce risks.
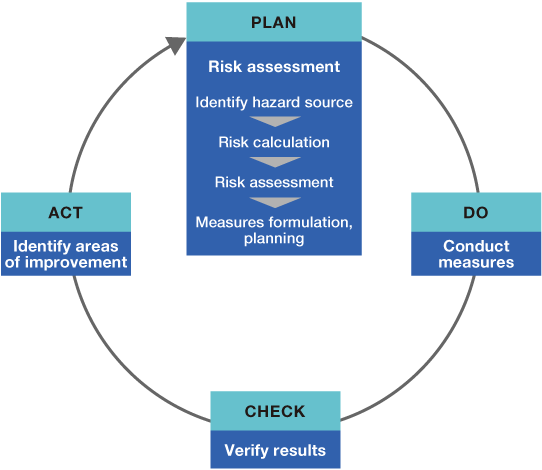
(2)Improve Security Level
Introduction of New Technology for Security and Accident Prevention Activities
In response to the Ministry of Economy, Trade and Industry (METI)’s promotion of safe use of drones in the plant security sector, JSR is considering the use of drones in its security and accident prevention activities with reference to the guidelines published by METI on the safe operation of drones outside of petrochemical plants.
In 2021, we conducted verification tests on the feasibility of using drones for aerial photography and conducting inspections on manufacturing facilities and tanks. We began reviewing an autopilot system to improve the efficiency of patrolling inside the Yokkaichi Plant.
The review of drone operations has been taken over by ENEOS Materials Corporation since April 2022 following the transfer of the elastomer business.
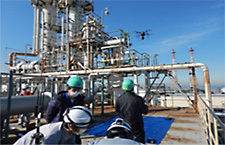
(3) RBPS-based Safety Audits
An auditing team led by the President regularly conducts annual Headquarters Environment and Safety Audits in plants and laboratories. From FY2015 onward, we have switched to an auditing style which incorporates sharing and discussion of the audited departments’ issues. On top of this, we have established opportunities for dialogue between top management and employees where both sides can share their thoughts with one another to rejuvenate environmental and safety activities.
In FY2021, audits were conducted on all JSR business sites (Yokkaichi, Chiba, and Kashima plants, and Tsukuba Research Laboratories) as with previous years. In light of the COVID-19 pandemic, audits were once again conducted online while on-site inspections were cancelled. The conditions at each business site were confirmed during the audit following the RBPS (risk-based process safety) approach on priority points. The number of feedback and requests categorized by each priority point are as follows.
Business site | Priority point | |||
---|---|---|---|---|
Risk awareness | Construction management | Risk management | PDCA | |
Yokkaichi | 1 | 3 | 5 | 0 |
Chiba | 0 | 1 | 4 | 0 |
Kashima | 0 | 3 | 6 | 1 |
Tsukuba | 0 | 0 | 2 | 0 |
Total | 1 | 7 | 17 | 1 |
Most of the feedback, requests for improvement and comments received during the audits pertained to “risk management” at all business sites. We believe this is due to our revision of the risk assessment procedures. As mentioned above in (1) Risk management implementation and advancement, we expect the breakdown of risks relevant to our business will further shift due to the transfer of the elastomer business. We will pay close attention to communicating with each business site and Group company, as well as continue to emphasize “risk management” in future safety audits in considering our response to changes.
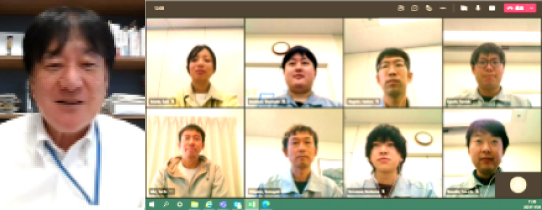
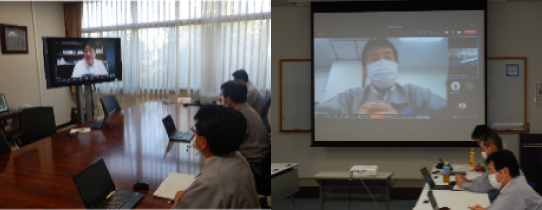
(4)Maintaining Certification Under Each Law
JSR Chiba Plant renewed its high-pressure gas certification in FY2021.
Following the transfer of the elastomer business, certification on the following will be succeeded and changed: <High Pressure Gas Safety Act> Accredited (Completion, Safety) Inspection Executor, <Fire Service Act> hazardous materials facility construction modification-related business site certification, and <Industrial Safety and Health Act> Class-1 pressure vessel operational inspection target sites for certification of boiler shut down inspection cycle. JSR Yokkaichi Plant has taken over the certification for <Fire Service Act> hazardous materials facility construction modification-related business site certification.
(Certification renewal in April 2022)
Other Activities
(1) Safety Culture Self-assessment
At JSR, we believe that effective safety is contingent upon an effective safety culture (system that fosters a culture which prioritizes safety) and safety infrastructure (system to ensure safety). In other words, we recognize that it is not only necessary to have safety infrastructure, but it is also essential to ensure a safety culture is being promoted.
As a metric for regular monitoring of the maturation of safety culture, we have created and implemented the use of self-assessment questionnaires. These questionnaires are distributed during each period of the medium-term management plan. As we have identified differences in scores concerning safety from the previous questionnaire (discrepancies between business sites, between managers and staff, and individual awareness), we are striving to penetrate safety related values through training.
On the other hand, along with the transfer of the elastomer business, major shifts are happening in areas such as our workforce composition. To properly address this issue, we plan to conduct interviews at each business site and Group company to identify the changes following the transfer and develop corresponding measures as appropriate.
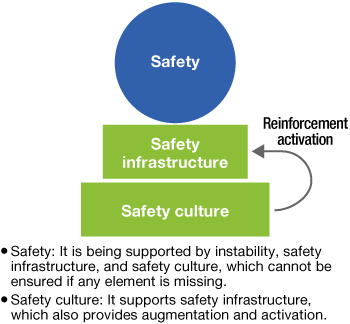
(2)Development of Safety Infrastructure
JSR has established regulations and procedures concerning security, accident prevention and occupational safety based upon our Security Management Regulations, which are organized in a manual to ensure thorough compliance with requirements stipulated in legal regulations. We have confirmed that these manuals continue to be adequate even after the transfer of the elastomer business.
In the meantime, we are reviewing the Risk Management Manual, which is used to protect stakeholders and minimize risks in the event of an emergency situation such as severe accident, disaster or scandal related to our business activity, as it is determined that a revision is necessary.
We prioritize the sharing of contents with business sites that are targets of the revision and verify its effectiveness through training. Training was conducted at a number of business sites in March 2022, through which we have confirmed there was no major deficiency following the revision of the manual. We will continue to conduct effectiveness studies to ensure the manual is functioning effectively.
(3) Preparations for Severe Natural Disasters
In preparation for large earthquakes, JSR has implemented aseismic construction with a focus on high-pressure gas facilities in its plants, based on the results of seismic performance assessments. At present, an earthquake early-warning system has been installed at all JSR business sites.
JSR is also reviewing its disaster prevention measures according to the needs of each business site due to the increased instances of severe and localized natural disasters that also cause catastrophic damages other than earthquake (flooding, high winds, typhoons, and tsunami).
In addition, we have established a system that enables us to promptly obtain updates on the situation of JSR Group in areas affected by severe natural disasters by determining the definition and communication routes for each.
We confirmed that there were no human injuries or damage to facilities at business sites located near the epicenters of the earthquake that hit the Kanto region on October 7, 2021 (maximum seismic intensity of 5 upper) as well as the earthquake off the coast of Fukushima Prefecture on March 16, 2022 (maximum seismic intensity of 6 upper).
(4) Investment in Safety
JSR continuously invests in safety, including countermeasures against occupational accidents and aging facilities. For details about our investments in safety equipment, please refer to “5. Investments in Environmental and Safety Equipment” under Initiatives to Prevent Pollution in the Environmental section.
4. Legal Compliance Management
(1) Legal Compliance Structure
JSR has established supervising departments and business execution departments for each law and regulation, and has identified laws, regulations, and ordinances applicable to occupational safety, security and accident prevention, as well as standards established at plants. To comply with legal revisions, we utilize the Law Revision Monitoring Service to prevent compliance related mistakes or omissions, and actively obtain information on national government circulars and revisions from organizations we belong to and local governments. The information we obtain is disseminated to employees in accordance with information sharing procedures.
(2) Legal Compliance Status
In FY2021, we have confirmed that there were no violations of laws on occupational safety, security and accident prevention at JSR.
5. Training
(1) Occupational Safety, Security and Accident Prevention Training
JSR conducts on-the-job training (OJT) at each workplace and offers experience-based, practical skills training in miniature plant setting at its company-owned and operated training centers. This training helps to instill knowledge, skills and sensitivity to security management. Training on work processes includes an experience-based component provided in a virtual space using virtual reality (VR). Through experiencing fear that is difficult to replicate in real life for safety reasons, employees are able to increase their safety awareness and make efforts to eliminate unsafe actions.
In addition to mandatory training under occupational health and safety laws, we provide training on occupational safety, security and accident prevention in rank-based training for each job type in stages. We hold regular meetings to discuss this training and continuously review the curriculum and approaches based not only on the views of top management, but also feedback from the frontline of operations and results of surveys given to participants and instructors after training.
In FY2021, we held training on common skills required for manufacturing plants 22 times with a total of 512 participants, including 454 from JSR and 58 from Group companies, covering a total of 7,494 training hours. In addition, we held training in a miniature plant setting at our training centers five times with a total of 49 participants, spanning a total of 135 training hours.
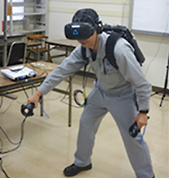
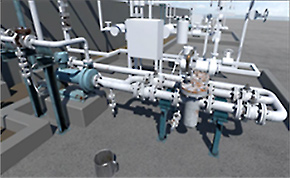
(2) Risk Assessment Training
We conduct risk assessment training to increase the accuracy of our risk assessments. Through risk scenario training, we have put into a place a system for developing HAZOP leaders and continuously implementing improvement activities.
In FY2021, we held training on how to prepare process hazard scenarios two times, with 19 participants (17 from JSR and two from Group companies), spanning a total of 285 training hours.
(3) Fostering Safety Culture Using e-Learning
In FY2021, we held e-learning for all JSR employee focused on our safety philosophy and basic policy on safety in order to foster a culture of safety. At 98.4%, the participation rate fell short of 100% because some employees were unable to participate due to system constraints. Nevertheless, the survey revealed that all employees who participated understood the curriculum.
Looking ahead, we plan to roll out this training globally at our Group companies outside of Japan to penetrate our safety philosophy and policy further.
6. Internal and External Communication
(1) Internal Communication (Entire JSR Group)
Safety Ceremony and Safety and Health Activity Forum
JSR believes that safety is linked to the daily lives of all stakeholders and is also the bedrock of the company’s management. With this in mind, we have made it a goal to achieve zero facility-related accidents and zero lost time accidents. However, a serious workplace accident which claimed the life of an on-duty employee occurred at the Yokkaichi Plant on July 23, 2014. In addition, there was a fatal accident involving an employee of a contractor working at the same location on May 14, 2020. With a pledge to aim for zero accidents and keep the lessons learned from these serious workplace accidents alive, and with a promise to continue developing a strong safety culture into the future to protect precious lives, we erected a safety monument in front of the Yokkaichi Plant’s main building and also hold a safety ceremony as well as a forum for presenting case examples of safety activities by business sites each year around the same time as these accidents.
In FY2021, we held the Safety Ceremony and the Safety and Health Activity Forum on July 20 live on the company’s intranet due to the COVID-19 pandemic. During the Safety Ceremony, a live video message from Executive Officer Takahashi was shared from the head office and a safety oath was made by two members of management including the head of the Yokkaichi Plant directly from the Yokkaichi Plant. At the Safety and Health Activity Forum, each business site made a presentation on good practices chosen based on a rigorous screening process from among the safety activities nominated by JSR and Group companies inside and outside of Japan. President Kawahashi also provided his comments from the head office.
This live format made the event accessible to employees of JSR and JSR Group who otherwise could not have attended, leading to many participants as compared to a typical year. As a result, we were able to directly convey our commitment to safety to a large number of employees.
The live stream was recorded and made available for later viewing on our company intranet by employee who could not participate on the day of the event.
In the future, the Safety Ceremony will be held by ENEOS Materials Corporation following the transfer of the elastomer business in 2022. JSR is considering establishing a new Safety Day in order to continue this same commitment.
Safety Ceremony and Safety and Health Activity Forum website
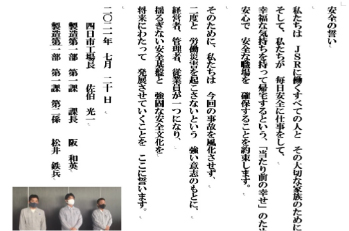
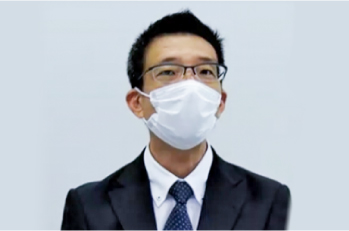
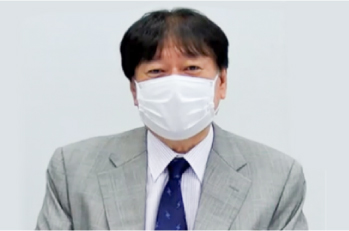
Presenting Group | Theme |
---|---|
JSR Yokkaichi Plant Production Dept. |
Safety activities using Unit Base and TEAMS |
JSR Yokkaichi Plant Research Center |
Establishment of smart inspection system using IoT sensors |
JSR Yokkaichi Plant Environmental and Security Dept. |
Workstyle innovation activities for security and accident prevention operations |
Kraton JSR Elastomers K.K. Manufacturing Section |
Issues and countermeasures for fostering a stronger safety culture |
(2) External Communication (Communities and Society)
JSR is a member of the Japan Chemical Industry Association, Japan Petrochemical Industry Association, the Japan Society for Safety Engineering, and Japan Industrial Safety Competency Center. Through the following safety activities and our Responsible Care program, we communicate with communities, society and peers, sharing information both in Japan and abroad.
- Hosting of or participation in accident prevention training drills of firefighting authorities and joint training with other nearby companies
- Participation in joint accident prevention organizations with nearby companies
- Participation in disaster prevention councils in the community
- Participation in local dialogue on Responsible Care
- Response to CSR surveys from other companies/organizations
Our business sites in Japan and overseas also actively communicate with their local communities to increase awareness of safety, improve safety technologies and reciprocally prevent accidents.