JSR, ANA and SHC Design Jointly Develop a 3D Printed Prosthetic Leg
It is estimated that approximately 17 million people(*) in developing countries need prosthetic legs after amputation of their lower limbs, not only due to conflicts and natural disasters, but also diabetes caused by imbalanced diets. Nevertheless, the prosthetic legs currently used are made of metal and are expensive, with unit prices ranging from approximately 3,000 to 4,000 USD. As a result, only a limited number of persons can purchase such prosthetic legs.
Even in developed countries, including Japan, those with prosthetic legs are forced to endure a wide range of inconvenience, especially when traveling. For example, concerned that the metal used to make their prosthetic leg might rust, they hesitate to approach the seashore, or to wear their prosthetic leg in a hot spring. In addition, when passing through a security check at an airport, the sensors react to the metal parts in an prosthetic leg. Therefore, users need undergo repeated examination and they are subject to pat-down inspections by security staff.
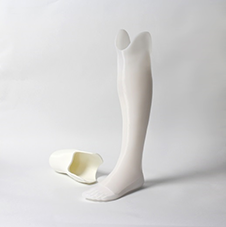
To relieve such trouble and frustration among prosthetic leg users both in and outside Japan, SHC Design launched the development of a new 3D printed prosthetic leg in 2015. The company strives to put this innovative product to practical use by utilizing the FABRIAL™ R series, materials developed by JSR for 3D printing.
With its target of a sales launch in 2017, the prosthetic leg is characterized as follows:
2) Manufacturing cost: approx. 20% to 30% of that of common prosthetic legs
3) Lighter weight than existing prosthetic legs, because no metal is used
Under a contract from the Japan International Cooperation Agency (JICA), SHC Design is currently conducting Survey on 3D Printed Prostheses Solution in the Philippines for the purpose of delivering lower-priced prosthetic legs to many more people than before. At the same time, in Japan, the company is aiming at business development with a focus on the use of its product as a “second prosthetic leg.” This will help relieve users’ mental and physical frustration during travel, and enable them to experience what they could not experience with their first prosthetic leg.
Endorsing these purposes of the innovation by SHC Design, ANA will cooperate with SHC Design from a wide variety of angles, including verifying the product by issuing ANA employees with prosthetic legs; providing technical advice; conducting demonstration experiments at airport's security check points; verifying the provision of services at airports; and providing support for SHC Design in traveling for business development purposes. By doing so, ANA will continue to enable many more passengers to enjoy comfortable flights. Meanwhile, JSR will provide support for SHC Design by providing the FABRIAL™series, 3D printing filaments developed together with the Social Fabrication Laboratory of Keio Research Institute at SFC (Director: Professor Hiroya Tanaka).
<FABRIAL™R Series>
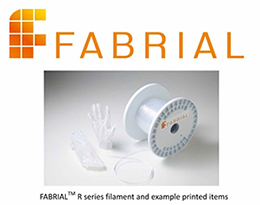
FABRIAL™series are 3D printing filament materials developed by JSR using its unique polymer technology. Major materials previously used for 3D printing had low strength. This caused various problems, such as breakages while processing and brittleness in finished items, making it difficult to put 3D printed items to practical use. The new materials used for the prosthetic leg have been developed based on materials that have been adopted in a wide variety of industries, including the medical field. These soft and flexible materials have enhanced the versatility of 3D printing in application and design, and realized the production of actual products. In addition, since these materials are used directly on the skin, safety has already been confirmed by a skin irritancy test (ISO 10993-10).
(*) Estimated by SHC Design based on information from the World Health Organization (WHO), 2016, “Global Report on Diabetes,” as well as from the website of the Japanese Society of Limb Salvage & Podiatric Medicine (http://www.jlspm.com/goaisatsu.html) (in Japanese)