Safety Assurance that Supports Materials Innovation
Chemical plants handle high-pressure gas and many hazardous materials. Should an accident occur, it may cause injury to employees and damage to not only equipment and products within the plant but also to the neighborhood. It may affect the supply of products as well.
Since its foundation, the JSR Group has been making vigorous efforts to ensure safety under the principle that safety takes priority over production.
Eliminating accidents and disasters
The JSR group has been striving to maintain and improve the level of our facility management, production technology, human resource development, and environmental conservation to ensure safe operations as shown in the chart below. The foundation of these efforts is our “safety culture.”
Safety culture is a safety-first climate that prevails throughout an organization from top management to each on-site worker. At the JSR Group, in order to build a more solid safety culture, it is assured that every employee shares the principle that safety takes priority over production and conducts safety activities on a daily basis to enhance the level of safety.
In FY2014, however, accidents which caused injury to JSR employees and manufacturing partner employees and resulted in absence from work occurred. We will review existing safety activities and identify and solve outstanding issues, and reconstruct a safety culture in which all concerned personnel including top management share the same safety principles, and in which safety is incorporated into all of our business practices.
(accidents resulting in lost work time)
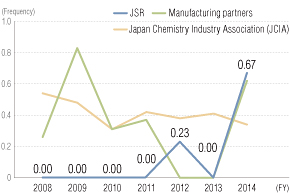
Frequency = (Death or injuries in industrial accidents resulting in absence from work/Total working hours for all employees) × 1 million
Safety target set under JSR20i6:
Reinforce the foundation for safety assurance at production sites to achieve zero facility accidents and zero worker accidents, resulting in no lost work time across the Group.

Act professionally with awareness and responsibility to assure safety
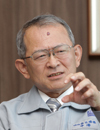
Senior Officer
Yokkaichi Plant Manager
It is essential to have sufficient knowledge of the materials handled, as well as to possess high operational skills to ensure the safety of chemical plants. At the Yokkaichi Plant, in order for employees to obtain these essentials, we spend significant time on safety training. However, despite this focus on training, we know that we cannot reduce the risk of industrial and facility accidents to zero no matter how hard we try. Keeping the forgoing in mind, we diligently conduct safety activities.
I continually emphasize that the level of safety assurance can be calculated by multiplying “skills” by “mindset.” Skills can be improved by each employee in carrying out their daily safety activities as well as by upgrading our risk prediction ability and technical knowledge. Even with adequate skills, accidents and injuries may still occur if employees are not well aware of the potential consequences of mistakes or lapses in the level of awareness or responsibility necessary of professionals working in a chemical plant. What I mean by “mindset” is a strong determination to observe the rules we have established and to put acquired skills into practice. It is indispensable that all employees have this mindset and these skills.
In FY2015, each section of the plant discussed important safety issues that need to be addressed and areas where more efforts need to be made. We then incorporated activities identified as being the most critical into their operational plans. It was assured that every employee in each section understood why their activities were important and showed strong determination to implement them. The progress of each plan will be regularly reviewed through plant manager safety audits.
Comments from external experts who visited the Yokkaichi Plant on May 28, 2014

Chemical complexes need to be located close to the sea. At the Yokkaichi Plant, the main administration building was rebuilt in consideration of the risk of a tsunami, for example, by opening the disaster control headquarters on the fourth floor and a standby power generator on the roof. Since safety is particularly important for chemical plants, I would like the plant to continue to pursue the enhancement of workers’ skills and mindset.
Keiko Suzue, PhD.Plant Manager Nakazawa told us that no matter how many manuals are prepared, these alone cannot reduce the number of accidents to zero. According to him, making steady efforts through the boosting of “skills” via having a “mindset” and, ultimately, each employee’s awareness and responsibility are key to minimizing accidents. These words were very impressive. I think this can be said not only for safety and the environment but for every aspect of corporate management. I hope this idea is passed on to global human resources as well during their training.
Mr. Hiro MotokiPlant Manager Nakazawa is very safety conscious, ensuring that basic measures are fully implemented throughout the plant, such as installation of emergency exits and safety aisles, the securing of access to fire hydrants and fire alarms, the wearing of protective equipment, and implementation of the 5S (Seiri (sorting), Seiton (organizing), Seiso (cleaning), Seiketsu (sanitizing) and Shitsuke (sustaining)) method. One point of improvement I would like to note is that there were no safety cautions given to us. There was no explanation as to whose instructions we should follow and where we should evacuate in the case of an emergency. Giving warnings or explanations is probably something that is done in daily operations, but it should preferably also be done also on special occasions such as at dialogue meetings.
Safety initiatives by global Group companies
The JSR Group operates production sites in various locations around the world. Since products handled and machinery and equipment used differ among the sites, each site needs to adopt a safety approach that best matches their own circumstances. Goals are set and measures are devised on a site-by-site basis to ensure that each of the respective site’s workers maintain high safety standards in their work practices.
JSR Engineering Co., Ltd.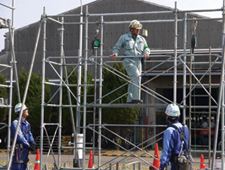
Recently in the chemical industry, frequent occurrence of industrial accidents during periodic maintenance and other non-routine operations has been seen. At JSR Engineering, a Group company that undertakes engineering work, training is provided periodically to workers engaged in construction and maintenance work at each plant to raise their sensitivity to possible dangers. In FY2014, an expert was invited from a temporary equipment rental company to provide training on scaffolding work to employees of the company and its business partners.
JSR Micro Korea Co., Ltd. (Korea)
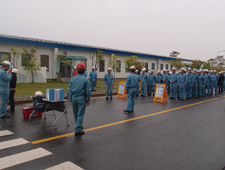
A drill for various disaster scenarios with the participation of all company employees is conducted twice a year in cooperation with the local fire station. Even on a divisional basis, training is provided to staff members on how to respond in the event of a disaster. The company also regularly checks disaster prevention facilities to make sure they will work safely during an emergency, and provides training to employees on the proper use of respirators and fire extinguishers once a year.
JSR Micro Kyushu Co., Ltd.

The company focuses on “individuals,” as the last and most important safety net, and makes it a rule to review close call incidents onsite in the presence of everyone concerned to enhance employees’ awareness of and sensitivity to safety with a view to eliminating all potential risks and creating a sound safety culture. The company has also been caring for employees’ physical and mental health by offering medical examinations by an industrial physician. These efforts have been recognized by external organizations, and in June 2013 the company received an award from the Commissioner of the Fire and Disaster Management Agency as an excellent site that handles hazardous materials, in addition to certification of the company’s effective occupational safety and health management system by the University of Occupational and Environmental Health in August 2013.
JSR Life Sciences Corporation
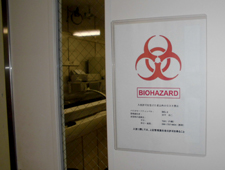
The biomedical business requires various unique safety activities. One such example is biohazard control. Experiments such as those producing proteins from cultured E. coli cells are evaluated for safety in advance using a different approach from that for chemical experiments and in accordance with biohazard experiment safety control standards. A biohazard mark (see the above photo) is also displayed on the door of the laboratory to restrict access depending on the level of hazard of the biomaterials used.
JSR Micro, Inc. (United States)
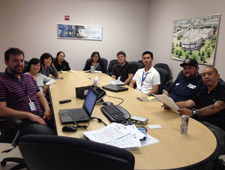
The EHS Committee takes the initiative in carrying out safety activities of the company, gathering safety concerns and proposals from different departments and conducting safety activity presentations to share the gathered information across the company. The committee members also meet every month to discuss safety inspection results and measures to address concerns and prevent hazards, as well as to verify the progress, current status, and effectiveness of the prevention measures taken. In FY2015, the company will use external consultants to utilize their opinions for its continuous improvement efforts.