Sustainability
JSR is committed to using value creation through business to
help achieve a sustainable environment and society.
Providing Value to Society through Our Business Activities
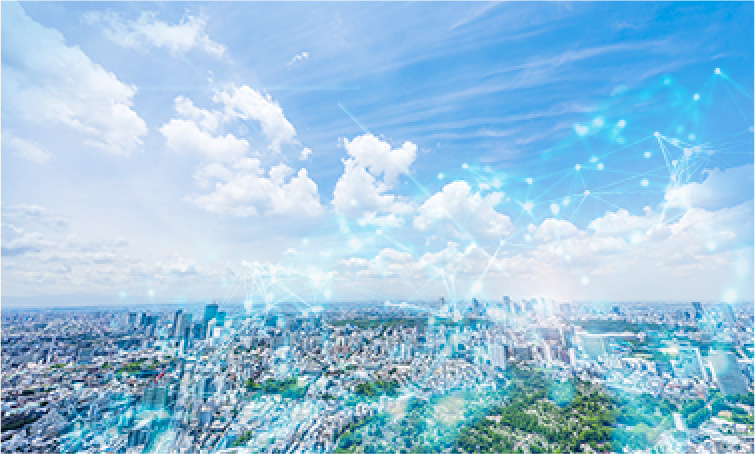
Contribution to Quality of Life and Happiness
Providing Materials That Support a Comfortable Society
Strengthening Our Management Foundation to Continue Providing Value
Latest Sustainability Information
- 05/12/2025
- Third-party verification of GHG emissions data
- 02/28/2025
- JSR received a B rating in two categories of the CDP 2024
- 12/20/2024
- JSR revamped its sustainability website.
- 06/05/2024
- A third-party verification opinion on GHG emissions results for fiscal 2022 was published. (PDF: 0.7MB)
- 04/24/2024
- Support for the people and areas affected by the 2024 Taiwan Coast Earthquake
- 04/01/2023
- JSR joins Japan Climate Leaders’ Partnership(JCLP) as supporting member.
(Japan Climate Leaders‘ Partnership Web Site) - 03/01/2023
- Support for the people and areas affected by the Turkey-Syria Earthquake